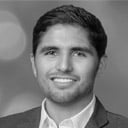
As a leading provider of construction asset management technology, Tenna takes pride in cycles of constant innovation. The newest releases from Tenna make equipment management even more productive by enhancing the amount and quality of data that can be obtained from assets and making inspections even more meaningful and actionable.
Using CAN bus technology for better data analysis and external PTO monitoring
Tenna’s new TennaCANbus tracker is an updated way to track heavy equipment. By installing the TennaCANbus on heavy equipment, users can now track and monitor idle time, fuel consumption, asset information, engine information, battery level, fault codes & decoded messages, environmental data, and tracker analytics—in addition to the location, utilization, and maintenance data previously collected.
CAN (Controller Area Network) or CAN bus is a widely used communication protocol that allows different electronic control units (ECUs) within a vehicle or piece of equipment to communicate with each other. It is a network protocol that helps data exchange between various systems—such as the engine, transmission, brakes, sensors, and more. CAN bus enables real-time, reliable, and robust communication, making it suitable for applications requiring extensive data coverage and integration between different machine components.
TennaCANbus enables construction equipment managers to make better decisions about rentals, replacements, preventative maintenance, and resource management. The tracker also makes it possible to track external power take-off (PTO), which enables the use of an asset’s engine power to drive added equipment or perform specific tasks. External PTO is often used to provide power to external accessories, including hydraulic pumps, generators, winches, compressors, and other types of equipment that require mechanical or electrical power to operate.
Tracking external PTO usage on vehicles and equipment can provide several benefits, including:
- Optimizing operational efficiency by supplying insights into how and when PTOs are used. This information allows fleet managers and operators to find opportunities for improved scheduling, task allocation, and resource management.
- Gathering data on the runtime and frequency of PTO engagement. This information allows fleet managers to implement preventative maintenance and service planning, ensuring prompt inspections, lubrication, and repairs to prevent unexpected failures and costly downtime.
- Making it easier to quantify the fuel consumption attributed to PTO engagement and find opportunities for fuel-saving measures. This knowledge can lead to more efficient route planning, task sequencing, and equipment choice—ultimately reducing fuel costs and improving the overall fuel economy of a fleet.
- Aiding in diagnostics and troubleshooting. If irregularities or issues pop up during PTO operation, tracking the usage data can help pinpoint potential causes.
- Accurately monitoring and documenting PTO engagement to ensure compliance with regulations and safety guidelines. Additionally, tracking PTO usage helps find potential misuse or unauthorized use of PTOs, promoting safety practices and preventing accidents or damage to equipment.
- Making it easier to accurately distribute costs and billing. By recording the duration and extent of PTO engagement, billing departments can generate precise usage reports and invoices, enhancing transparency and ensuring fair billing practices.
Overall, tracking external PTO usage supplies valuable data that enables informed decision-making, improves efficiency, reduces maintenance costs, enhances safety, and streamlines operations for vehicles and equipment that use PTO-driven functions.
TennaCANbus is poised to be a game-changer for construction companies trying to achieve greater productivity, efficiency, and business growth. Maintenance, diagnostic troubleshooting, and service planning are made easier with more information on runtime and frequency of PTO engagement. Fuel use and idling metrics give a more comprehensive picture of where waste and excessive wear and tear are occurring. Understanding more about how heavy equipment is being used, including when PTO is engaged, can simplify reporting around compliance with safety regulations and improve billing by making the distribution of costs more accurate.
More meaningful and actionable inspections with Custom Inspections add-on
A critical part of fieldwork involves equipment inspections ensuring safe equipment performance, and finding hazards or maintenance and repair needs. Tenna’s equipment inspections allow teams to perform inspections in the field with Tenna’s unique QR-code-based functionality. These digital inspections replace paper-based methods, making it easier and more efficient and resulting in a higher likelihood of inspection completion. But we’ve also heard about special needs, such as certain assets more prone to leaks or assets on specific job sites collecting a lot of external damage.
With Tenna’s Custom Inspections premium add-on to the Safety & Compliance license, users can create custom inspection forms that are as specific as needed to make inspections more insightful.
The new Custom Inspections add-on allows users to create inspections specific to job sites, use cases, or types of equipment. They can also mandate custom fields and signatures, and instantly apply new forms to all applicable assets. Inspection items can also be grouped into a site-specific logical order for a more efficient process in the field.
With the launch of these new products—as well as ongoing enhancements to existing features—Tenna continues to prove its commitment to helping construction companies grow and succeed while improving safety and productivity.
Schedule a demo today to learn more about adding TennaCANbus and Custom Inspections to your construction business.
About Jose Cueva
As Chief Product Officer and Co-Founder, Jose applies his first-hand construction experience and knowledge to deliver innovative platform solutions to a growing number of companies. His involvement in both architecting construction-specific solutions and delivering them enables him to cross over functional roles.