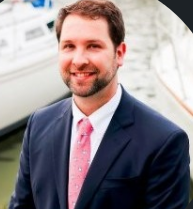
Updated Jan 27, 2025
The construction industry is no stranger to challenges in managing parts inventory, maintenance and R&M cost tracking. A misplaced wrench can halt progress, while an unexpected parts shortage can send project schedules spiraling. With numerous moving parts—literally and figuratively—keeping track of equipment, tools and materials can be overwhelming.
This is where parts inventory management software for construction comes into play. Digitizing the parts requests and inventorying process offers powerful solutions to streamline all parts of maintenance operations that rely on, well, parts.
Without software to help centralize and streamline, contractors miss important data on their business and likely lose track of parts and money along the way.
Benefits of Digitizing Parts Requests and Inventory Management
Modern parts inventory management software for construction businesses offers a centralized, digital hub for tracking the location and exchange of every nut and bolt. Here are some of the benefits.
Digitizing the parts allocation process gives real-time tracking of parts. It improves record keeping and organization, and this helps construction businesses stay ahead and avoid losing money.
Parts inventory management software also helps contractors track the quantities and availability of important parts to support maintenance activities and keep maintenance schedules on time. It removes the guesswork about what parts are available, when they are needed, and where to find them.
Here are some of the key benefits of inventory management software for construction:
- Real-Time Inventory Tracking: See what parts and materials are in stock in the contractor’s warehouse via a digital parts catalog, including quantities and location for visibility and insight on when to restock them.
- Unblock Maintenance Activities: Schedule and manage equipment maintenance seamlessly with available parts, reducing unnecessary downtime.
- Cost Control: Minimize unnecessary purchases and losses by optimizing inventory levels.
- Low Inventory Alerts: Receive automatic notifications when stock levels are low, ensuring uninterrupted operations.
- Parts Utilization Tracking: Monitor how parts are used, which machines they go to, and the sites they are most frequently sent to. This helps improve inventory turnover and reduce waste.
- Part Warranty: Recognize hard dollar savings through improved part utilization and warranty tracking—for every part of every machine.
- Save Time in the Field: Improve the parts request process for mechanics in the field. Even if they are not involved in the purchasing process, it provides a shortcut to see whether a part is in stock internally or needs to be sourced externally.
Addressing Common Challenges in Construction Inventory Management
Parts and inventory mismanagement can lead to project delays, increased costs and frustrated teams. Construction companies that stock parts internally often struggle with:
- Stock Shortages: Running out of essential parts can halt progress.
- Overstocking: Excess inventory ties up capital and occupies valuable space.
- Inaccurate Records: Manual tracking methods are prone to errors, leading to inefficiencies.
By digitizing the parts request, stocking and selection process, contractors can see what parts they use across all sites and warehouses. They can also identify what parts they need and which ones cost them more over time.
When you know what you have, you can:
- Better plan for preventative and predictive maintenance.
- Manage work orders more efficiently.
- Minimize costs and unnecessary ordering.
- Reduce equipment downtime.
- Save time in the field and the shop
Features like automated alerts, detailed reporting, and mobile accessibility ensure that teams have visibility and can make informed decisions anytime, anywhere. Additionally, monitoring parts utilization and providing comprehensive inventory insights allow businesses to fine-tune their operations and improve their bottom line.
Streamline Communication and Parts Coordination Between Field, Shop and Office
With a digital parts catalog that streamlines the inventory requesting process, construction companies can better connect the field, shop, and office. As a result, operations run smoothly with better visibility and without delays caused by poor communication.
Curious how this works? Here’s how Tenna’s Parts solution streamlines communication and parts information between teams:
- From the field, mechanics can ask for one or more parts needed for repairs. They can request these parts from procurement for the shop to review and submit. Plus, a digital catalog helps field mechanics know if they are choosing the right part for their repair. It also improves their understanding of the inventory that supports their work.
- From the shop, mechanics can take parts from inventory for a work order or maintenance request. They can use parts in stock as identified in a digital parts catalog and identify the parts that need to be procured externally.
- At the office, parts and procurement managers can keep track of parts’ costs, transactions and moves across locations via a Parts Consumption Report. This report shows how much they spend on parts for a single machine or asset category. (Did you spend $10,000 or $100,000 on transmissions last year?)
Construction equipment maintenance software, like Tenna’s, makes it easier to capture parts requests from the field or shop. This helps companies improve their procurement process. It works for both centralized procurement and on-demand purchasing by connecting different departments.
Choosing the Right Software for Your Equipment Maintenance Needs
Not all inventory management software for construction is created equal. Contractors should look for solutions that:
- Offer mobile access for on-site teams.
- Provide customizable reporting and analytics.
- Feeds into a maintenance management system.
- Offer robust tracking for parts utilization and inventory insights.
- Integrate with project management and accounting systems.
Streamline Maintenance and Reduce Costs with Parts Inventory Management Software 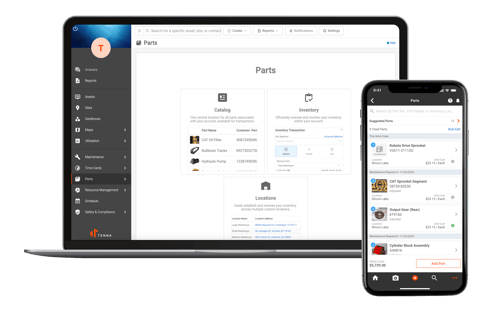
Using parts inventory management software built for the construction industry is not just a tech upgrade. Leveraging this technology is a smart step towards better operational efficiency and growth and improved repair and maintenance tracking. By optimizing your inventory and maintenance processes, you can ensure your projects are uninterrupted by maintenance delays, reduce waste and excessive costs, and stay competitive.
By digitizing the parts inventory process in your construction company, you’ll have access to real-time information to help drive data-driven decisions. Not only will you be able to analyze parts usage, but you’ll be able to track costs per maintenance requests and optimize ordering strategies to maximize your savings, strategically.
Interested in exploring Tenna’s parts inventory management software for the construction industry?
About Ryan Lunar
Ryan is the Director of Sales - East at Tenna. With nearly 10 years of experience in the GPS and IoT space, Ryan spends a majority of his time working with clients to understand their needs as an organization and align the appropriate solution. No two contractors are alike, and each require a unique solution to reach their desired outcome. Firsthand experience working in the field with partners and prospects helps Ryan and the Tenna team truly understand what it takes to serve the construction industry.