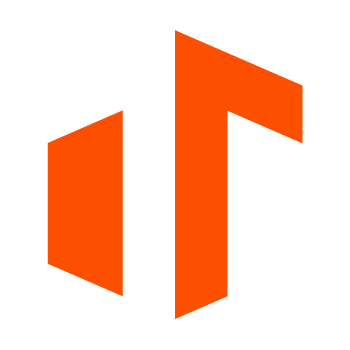
Maintaining an equipment fleet is one of a construction business’ biggest capital investments. However, many contractors find being conscious of the cost of owning and operating construction equipment expenditures to be one of the most challenging aspects of their operations. Fortunately for the construction industry, today’s construction-focused technology is built to help contractors better understand and manage construction equipment operating costs through continuous tracking, logging and monitoring, so they can make smarter decisions around expenses and planning.
Construction technology delivers ROI in so many ways. It enables control over resource management, better oversight for safety and compliance needs, full visibility over job costing, equipment utilization, risk management, and more—without ever needing to interrupt the flow of work in the field. In fact, it also brings efficiency to personnel through means of less manual work, less re-work, and all-around better tools to get the job done.
However, it’s important for contractors to strategize when choosing and leveraging construction technology. Tenna has identified five tips contractors should consider when building out their equipment management strategies as well as how to best utilize construction technology to lower construction equipment operating costs.
Read on for a sneak peek of these tips and what more we'll cover in our e-book 5 Ways to Lower Your Construction Equipment Operating Costs.
![]() |
Know what equipment you own |
It seems obvious, but knowing what you have saves you an incredible amount of time and money. You’re able to stay on top of the assets you already own, produce the right asset for your job, and better utilize and glean more value out of the assets you’ve already purchased. But, like most things in construction, this is much easier said than done.
Without a system to tell you where your equipment and tools are, contractors end up buying or renting assets they’re unable to locate or didn’t realize they already have. This leaves them paying unnecessary costs to acquire a new asset while their existing asset continues to sit idle burning a hole in the balance sheet—while also paying thousands of dollars each month against the loan on it.
Sound familiar? In this e-book, you'll learn how to gain visibility and control through construction equipment management technology and make more cost-effective equipment moves.
![]() |
Monitor how often your equipment is used |
Knowing what you own is important, but a close second in lowering construction equipment operating costs is being able to anticipate the life of your machines so you can maximize them while you own them. When you integrate an equipment fleet management system with telematics into your equipment tracking and management process, you can use the real telematic data from your machines to check your utilization and measure against benchmarks that you set for each piece of equipment.
Knowing your accurate equipment utilization can help you better establish benchmarks and thresholds for other machines, and new machines you add to your fleet to help maximize their useful life and earn you an ROI based on your construction equipment operating costs. Plus, knowing your true utilization helps you maintain the size of your fleet appropriate to your operational needs.
Exactly how can you measure utilization? This e-book will outline the impact of hoarding equipment and the impact of inaccurate utilization data on bid rates, and explain how an equipment management system can straighten out both.
![]() |
Ensure proper maintenance of your machines |
It’s obvious that repairs and routine maintenance amount to a high percentage of your construction equipment operating costs. Effective construction equipment maintenance extends your asset’s lifespan, improves performance and reliability, increases your ROI on your owned assets, and helps reduce or slow depreciation. Equipment management systems can automate preventive maintenance based on your defined triggers, so maintenance needs are always visible and scheduled for your mechanics.
With efficient maintenance, repairs caused by poor maintenance and/or neglect are reduced, lowering unnecessary construction equipment operating costs. Plus, you avoid unplanned downtime, which has direct impacts on your jobs. When your job loses money because of a machine, you eat at your margins. The more maintenance your machines need because of inefficient use or excessive wear and tear or frequent use outside of “normal working conditions,” the higher your parts and labor costs will be.
We’ll get into more details in our e-book including dollar amounts you could be saving just by leveraging a construction-specific technology solution.
![]() |
Proactively inspect equipment for safe performance |
Even with perfect maintenance, the construction environment is rough on equipment and damage is sometimes unavoidable. Construction equipment inspections help identify when something is amiss with a vehicle or machine and can keep the focus on and optimal performance. When an issue is discovered during a routine, pre-use inspection, a fix can be identified and taken care of quickly, before the issue or condition becomes worse or results in a costly and avoidable safety incident.
Equipment inspections may also sometimes shed light on operator misuse, which can become very costly in terms of machine maintenance and repairs. Repairs can cost thousands of dollars and reducing them across your fleet can save hundreds of thousands.
This e-book will reveal how you can get and stay in control by integrating technology into your inspection process as well as four ways it can help lower your insurance premiums.
![]() |
Track fuel consumption |
All your engine-operated assets need fuel to run. Fuel is costly to begin with based on industry prices and your level of use, but it can also be more costly than necessary based on operating behaviors. Recognizing your idling behaviors using telematics data from your machines interpreted by your equipment management system and curbing this practice in the field can help get a handle on construction equipment operating costs and increase resale value.
If you stop running up unnecessary hours on your machines with excessive idling, you’ll naturally also stop spending excessive amounts in fuel costs. Plus, reducing your idling costs also helps lower your maintenance costs—a win-win with the right technology in place. Reducing the amount of idling on a machine directly reduces the amount of maintenance needed on it instead of inflating the number of false operating hours racked up by idling.
Your assets may be costing your company millions due to idle time, but the good news is, this e-book will explain how construction technology solutions can help monitor and reduce construction equipment operating costs.
Download eBook |
About Tenna
Tenna is the construction technology platform powering equipment fleet operations. Beyond tracking, Tenna connects every aspect of fleet management, giving contractors a full-picture view of their equipment operations and a greater understanding of equipment trends, so they can increase productivity and reduce costs. With more than 100 years of construction experience, Tenna helps contractors maximize their mixed fleet with industry-focused solutions that connect field, shop and office to optimize all aspects of equipment management. For more information, visit www.tenna.com.