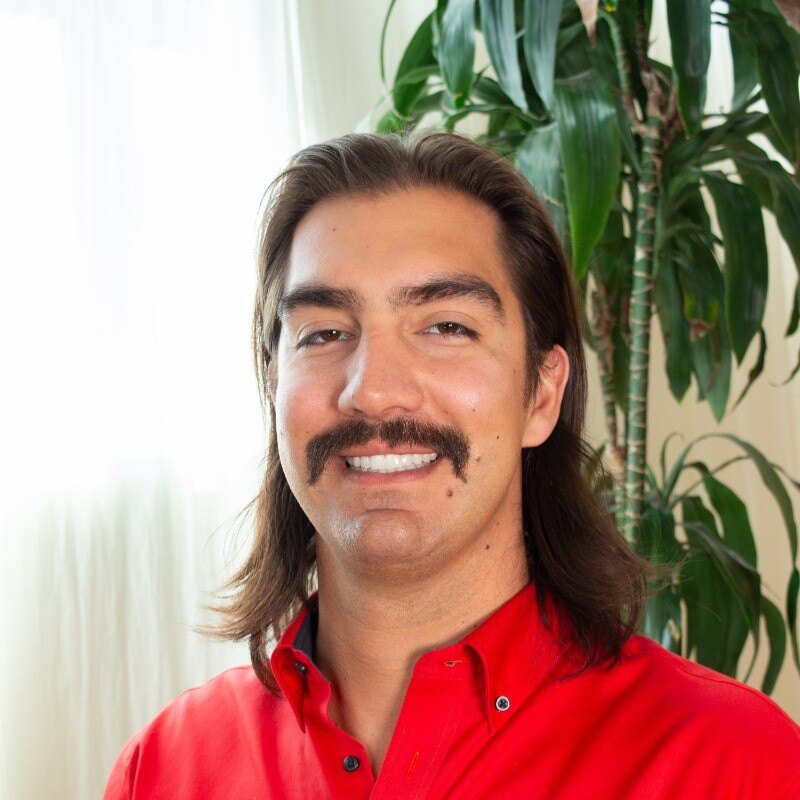
In the construction industry, where projects often run on tight schedules and heavy machinery plays a pivotal role, equipment reliability is crucial. If you're a contractor, you know that any unplanned downtime can cause significant delays. It can also increase your projected costs and seriously affect project outcomes.
This is why at the heart of a well-running equipment management program is equipment maintenance. Construction businesses rely on a wide range of equipment — from excavators and cranes to bulldozers and backhoes — all of which require regular maintenance to function efficiently. However, manually tracking maintenance schedules, usage data and service history can be very overwhelming.
This is especially true when it comes to large fleets that include owned and rented equipment from multiple manufacturers. How are contractors supposed to keep track of all their equipment maintenance schedules and needs?
This is where equipment maintenance tracking software becomes essential. By integrating equipment fleet tracking with maintenance software in one platform, contractors can automate and optimize maintenance processes.
Why Maintenance Tracking Matters
Even minor equipment failures can lead to major setbacks. A single machine going offline can stall an entire project, leading to costly delays and frustrated clients. How can maintenance tracking software minimize these risks? By:
- Automating maintenance schedules based on usage hours, mileage, or time intervals.
- Reducing human errors associated with manual tracking.
- Providing real-time alerts for upcoming maintenance needs.
- Extending equipment lifespan through proactive care.
By integrating technology into an equipment maintenance strategy, contractors can ensure machinery remains operational, safe and compliant with industry regulations.
Key Benefits of Equipment Maintenance Tracking Software
Implementing equipment maintenance tracking software delivers a range of benefits that directly impact your bottom line and operational efficiency.
Proactive Maintenance Scheduling
Imagine schedules for routine maintenance being automatically determined based on manufacturer recommendations, usage data, or time intervals. This proactive approach is attainable with equipment maintenance tracking software.
With these tools, construction companies can avoid unexpected breakdowns, reduce downtime, and ensure equipment is always ready for use. Plus, software like Tenna’s sends alerts to mechanics and the equipment team when repairs are due. Service statuses are updated as work progresses in the shop.
Real-Time Equipment Monitoring
With real-time monitoring from asset trackers, construction managers can track equipment health, location and usage metrics on one integrated platform. This quick access to data enables nimble responses to potential issues before they escalate into major problems.
Equipment maintenance tracking software can alert the shop of issues including fault codes for heavy equipment and diagnostic trouble codes for vehicles transmitted by GPS tracking devices on the equipment. Issues provided by the machine’s electronic control unit (ECU) help the shop understand the codes and root causes of the issue. This speeds up maintenance work orders and gets machines back to work faster.
Comprehensive Maintenance Records
Equipment maintenance tracking software like Tenna’s keeps detailed records of all maintenance tasks, such as oil changes, inspections, part replacements and more.
Equipment managers can identify upcoming service needs for each asset. They can also analyze scheduled repairs for all assets. This helps improve project workflows.
Plus, having this data easily accessible ensures compliance with safety regulations and simplifies audits. This ensures efficient record keeping, which can also help during equipment resale.
By adopting Tenna's equipment maintenance tracking software and GPS asset trackers, Shoring Engineers saved between $50,000 and $120,000. With Tenna, the contractor could see real-time location data and maintenance alerts, which helped them manage their equipment fleet better.
Equipment Cost Reduction
Consistent, scheduled maintenance reduces the likelihood of costly emergency repairs. It also extends the life of expensive equipment, providing better returns on investment. But how do you track this?
With equipment maintenance tracking software, contractors can monitor spending on labor and materials. They can use customizable cost codes to see what is really being spent on equipment maintenance and repairs. They can leverage parts inventory management to see what parts are in stock for better decisions around purchasing and controlling costs across business locations.
Enhancing Preventive Maintenance with Asset Tracking
Combining asset tracking technology with equipment maintenance tracking software creates a powerful tool for construction companies. Asset tracking—using GPS telematics—provides real-time data on equipment location, usage and performance. By integrating this data into a maintenance tracking system, contractors can streamline workflows and enhance preventive maintenance efforts.
Accurate Equipment Location
On large construction sites, finding the right piece of equipment for maintenance can be time-consuming. GPS asset tracking allows maintenance teams (among others in the field) to pinpoint exact locations, reducing time searching, equipment downtime and improving overall efficiency.
Equipment Utilization Insights
By analyzing usage patterns, construction managers can identify underused or overused equipment. This equipment utilization information helps schedule maintenance during idle periods, minimizing disruption to ongoing projects, while also reducing site hoarding and helping estimators build more accurate bid rates.
Automated Maintenance Alerts and Notifications
Asset tracking systems can trigger automated alerts when equipment reaches specific usage thresholds or exhibits signs of potential failure. These alerts ensure that maintenance teams perform tasks promptly, reducing the risk of major breakdowns.
Reducing Downtime and Costs with Predictive and Preventative Equipment Maintenance
Downtime is the enemy of profitability in the construction industry. Every minute a machine is offline translates to lost productivity and increased labor costs. Equipment maintenance tracking software helps construction businesses avoid this by enabling predictive and preventive maintenance strategies.
Using Equipment Data to Prevent Failures
Predictive maintenance leverages construction data analytics to identify patterns that signal potential equipment failures. For example, excessive fuel consumption, overheating or unusual vibrations can all indicate an impending breakdown. With construction equipment maintenance tracking software, shop teams can intervene before the issue worsens, preventing costly repairs and project delays.
Streamlining Resource Allocation
With complete visibility into equipment status and maintenance schedules, project managers can plan resources more effectively. They can ensure that equipment remains operational during important project phases. This helps avoid extra rental costs by using in-house machinery more.
Managing Spare Parts and Inventory
Unexpected breakdowns often require parts that aren’t readily available, leading to extended downtime. Maintenance tracking software should have parts inventory management features. This helps construction companies keep important spare parts in stock. It also reduces wait times for repairs.
Selecting the Right Equipment Maintenance Tracking Software
Not all equipment maintenance tracking software is created equal. Construction businesses need solutions that cater to the specific demands of managing large, diverse fleets and dynamic project environments.
Key Features to Look For:
- User-Friendly Interface: Field technicians and maintenance managers need intuitive tools that require minimal training.
- Mobile Accessibility: Construction sites are mobile, so your maintenance software should be too. Mobile access allows teams to update maintenance logs, access equipment data, and receive alerts from anywhere.
- Integration with Telematics and ERP Systems: Seamless integration with existing telematics systems and enterprise resource planning (ERP) platforms ensures that maintenance data flows smoothly across your entire operation.
- Customizable Maintenance Schedules: Every piece of construction equipment has unique maintenance needs. The right software allows for flexible scheduling based on time, usage and manufacturer guidelines.
- Real-Time Reporting and Analytics: Detailed reports help construction companies spot trends, improve maintenance strategies, and make smart decisions.
Keep Construction Projects on Schedule with Maintenance Tracking
For construction businesses that tightly control project timelines and budgets, equipment reliability is non-negotiable. Using equipment maintenance tracking software helps companies reduce downtime, lower repair costs, and extend the life of important machines.
By integrating asset tracking, leveraging predictive maintenance, and automating maintenance schedules, construction companies can enhance operational efficiency and ensure their equipment remains project ready. And in an industry where time truly is money, this is the key to staying competitive and profitable.
⬅️ To learn more about Tenna’s construction maintenance tracking software, contact us.
About Noah Hernandez
As a Tenna Regional Account Executive based out of Denver, Colorado, Noah gets to help show contractors that their workdays can be more streamlined, their business can save money and time, and equipment can be utilized more efficiently with Tenna's equipment management software. With years in the industry, he has proven to have a passion for helping those in the construction industry with connecting their needs with modern technology solutions.