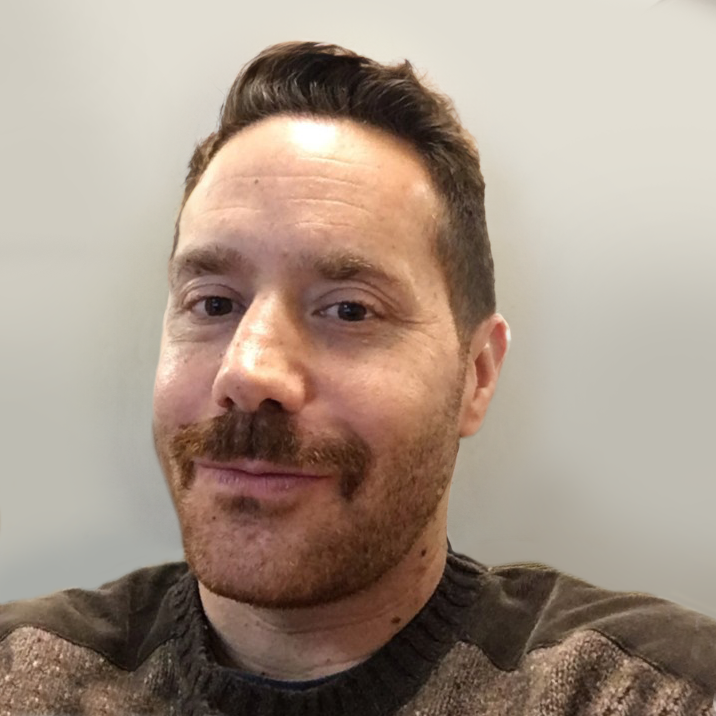
In the construction industry, construction equipment isn’t just a tool—it’s a significant investment that plays a crucial role in project success. Managing assets properly can mean the difference between profitability and unnecessary expenses.
When maintenance is overlooked, the consequences can be severe. Unscheduled breakdowns lead to unplanned expenses, project delays, and safety risks. Studies show that reactive maintenance can be three to five times more expensive than a planned maintenance strategy. Emergency repairs, lost productivity, and even higher insurance premiums because of equipment-related accidents all contribute to ballooning costs.
Beyond immediate expenses, poorly maintained equipment depreciates faster, requiring early replacements and higher capital expenditure over time. Contractors who ignore maintenance often face problems. Machines can break down when people need them the most. This leads to costly solutions, like renting replacement equipment.
A proactive approach to equipment maintenance helps machines last longer. It also reduces costly downtime and boosts project efficiency, which leads to a better return on investment (ROI). But with all that contractors are juggling; how can they attain a proactive strategy? This is where construction equipment maintenance software comes in.
A Proactive Approach to Equipment Maintenance
Rather than waiting for breakdowns to occur, smart contractors implement proactive maintenance strategies to preserve their investment using construction equipment maintenance software. A well-structured equipment maintenance program should include:
- Preventive Maintenance: Scheduled inspections, oil changes, filter replacements, and component checks prevent minor issues from escalating into major failures.
- Predictive Maintenance: Using data from equipment sensors helps monitor wear and tear in real-time. This can predict when you need to service it before a failure occurs.
- Routine Inspections: Daily and weekly checks should be performed by operators to identify and report issues early.
- Work Order Tracking: A clear system for managing maintenance requests and tracking completed repairs ensures accountability.
- Mechanic Time Tracking: Clear labor tracking helps contractors see how much mechanic time adds to total maintenance costs.
- Parts Inventory Management: Efficient parts tracking and management ensures visibility into in-stock inventory across locations. This enables teams to request and complete repairs timely and correctly.
- Cost Code Tracking: Aligning equipment cost codes with ERP and accounting systems helps contractors can gain complete understanding of costs attributed to projects.
Leveraging Technology for Smarter Maintenance Management
Modern construction firms are increasingly turning to digital solutions to manage equipment maintenance efficiently. Equipment tracking and maintenance management software provides real-time visibility into equipment condition, upcoming service needs, and historical maintenance records.
Features like automated maintenance alerts, tracking mechanic work orders, and telematics integration help improve operations. Additionally, construction equipment maintenance software should include features such as:
Automated Maintenance Scheduling: Reduce the risk of human error and missed service intervals. By automating maintenance tasks, this software reduces the risk of unexpected breakdowns. It prevents delays in your projects.
Real-Time Equipment Health Monitoring: Gain insights into wear patterns and performance to make data-driven maintenance decisions. Cloud-based solutions let you access data in real-time. This helps you make quick decisions and stay updated while on the move.
Centralized Record-Keeping: Ensure compliance with regulatory maintenance requirements and track trends in equipment reliability. This helps record all equipment-related information for easy access and management.
Comprehensive Reporting Tools: With access to reporting capabilities, contractors can gain insights into equipment performance and maintenance history. They can also see trends around asset types, jobsites, parts requests, and more.
Mobile Access to Features: Mobile access to software is important for field teams. It allows them to update and get information quickly with real-time data sharing. Teams can collaborate effectively, regardless of location.
Case Study: Severino Trucking
Severino Trucking is a civil construction contractor focused on highway and site development. However, they had trouble tracking and managing their fleet well. With equipment spread across multiple job sites, they needed a solution to improve visibility and control maintenance costs.
By implementing Tenna’s asset tracking and maintenance management system, Severino Trucking:
- Recovered Lost Equipment: Located $40,000 worth of equipment that was previously unaccounted for.
- Reduced Rental Costs: Saved $25,000 annually by improving fleet utilization and reducing unnecessary rentals.
- Improved Decision-Making: Real-time data allowed for better resource allocation, optimizing fleet efficiency.
Tenna’s solutions helped Severino Trucking streamline maintenance, reduce equipment downtime, and save money—directly impacting their bottom line.
Why Implementing Construction Equipment Maintenance Software Matters
Many contractors operate under the assumption that repairs are just a cost of doing business, but that is not the case. Here are some of the ways implementing an equipment maintenance software can make a positive impact on your business:
Here’s how it can make an impact on your business:
- Lower Repair Costs: Fixing a small issue before it turns into a major problem is always cheaper. Regular inspections and equipment monitoring through telematics help find wear and tear early. This prevents major failures that need costly repairs or full replacements.
- Extended Equipment Lifespan: Construction equipment is built to last, but only if it’s properly maintained. Following the manufacturer's maintenance recommendations helps keep your machines in great shape for years. Maintenance software enables contractors to set up pre-determined preventative schedules.
- Minimized Downtime: When equipment breaks down suddenly, it can stop work on a job site. This can cause project delays, extra costs, and penalties. Proactive maintenance management keeps machines operational and reduces unplanned downtime.
- Improved Safety Compliance: Equipment failures can lead to serious safety hazards. Regular maintenance makes sure all parts work well, which lowers the chance of accidents and keeps workers safe at work. Plus, by using an equipment management system, you’ll always be sure to keep compliance requirements up to date.
- Higher Resale Value: Well-maintained equipment retains value better over time. If you plan to sell or trade your machinery later, keep detailed, digital maintenance records with maintenance software. This will help you get a higher resale price.
The Long-Term Financial Benefits of Equipment Maintenance
Investing in construction equipment maintenance software isn’t just about staying on schedule and avoiding breakdowns. It’s about ensuring financial sustainability and long-term profitability.
By leveraging a maintenance software integrated with your equipment management system, contractors can:
- Increases Asset Productivity: Keeping equipment operational ensures projects stay on schedule and labor costs remain controlled.
- Reduces Total Cost of Ownership: Preventive maintenance minimizes emergency repair expenses and extends equipment lifespan.
- Enhances Resale Value: Well-maintained machinery commands higher prices on the resale market, recouping more of the initial investment.
- Boosts Job Site Efficiency: Fewer breakdowns mean less time wasted, improving overall productivity and profitability.
Other Considerations When Choosing a Technology Provider
For construction businesses wanting to boost long-term ROI, construction equipment maintenance software is an investment, which is why selecting the best construction equipment maintenance software requires careful evaluation.
Start by identifying your specific needs and challenges.
Consider the software's scalability with your business.
Choose technology with a user-friendly interface for better adoptability amongst employees.
Ensure the provider offers ongoing support and training to your team.
Evaluate integration capabilities so the software smoothly connects with existing construction management tools.
In a competitive industry where margins matter, smart maintenance decisions can be the key to sustained profitability. Companies that manage their equipment maintenance with technology today will lead in efficiency and success in the future.
-
Don’t let breakdowns continue to impact on your bottom line.
Contact us to take your maintenance program to the next level.
About Jason Mercury
As Customer Success Enablement Manager with Tenna, Jason Mercury excels at bridging the gap that exists between customers and their success with new technologies. He thrives on helping partners recover revenue and create efficient business process with construction technology, and has been instrumental in driving customer and internal team training, leading to invaluable positive results across the board.