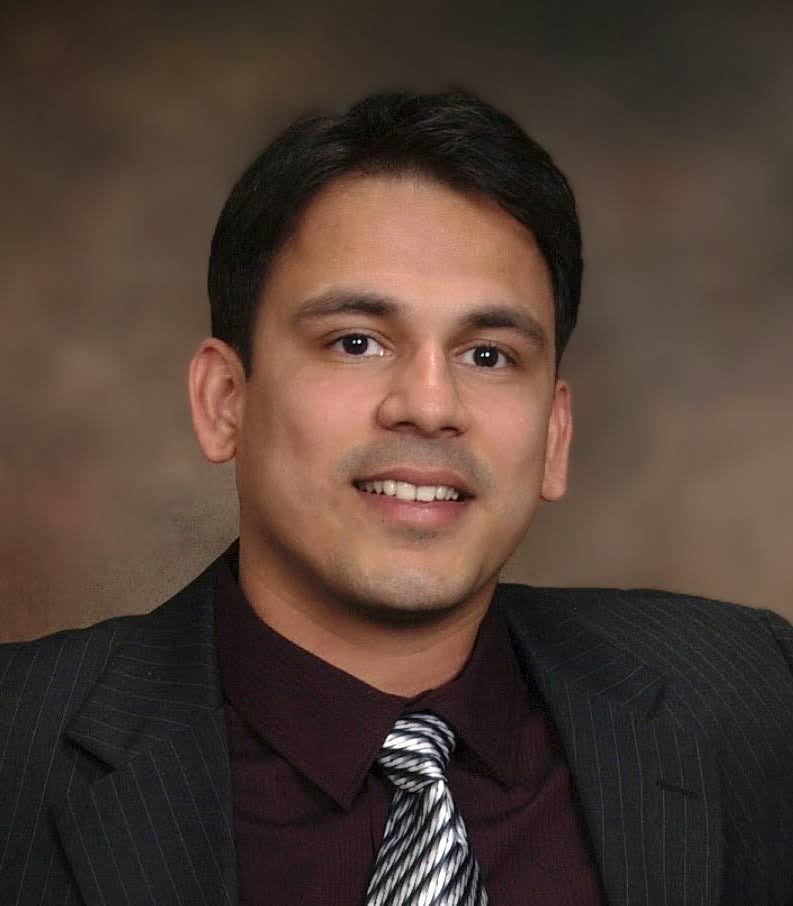
The world of construction technology is filled with acronyms: IoT, MRO, ERP, ELD, RFID, BLE, and the list goes on. But three specific acronyms make a world of difference when figuring out the type of data that can be extracted from vehicles and equipment—OBD, JBUS, and CAN bus. Let’s walk through what makes them different and the benefits of using CAN.
What’s the difference between OBD, JBUS, and CAN bus?
CAN bus, OBD, and JBUS all involve ways to allow sensors and systems used in automobiles and equipment to communicate data, but they have distinct differences and applications. Here's a breakdown of each:
CAN (Controller Area Network) or CAN bus
CAN bus is a widely used communication protocol that allows different electronic control units (ECUs) within a vehicle or piece of equipment to communicate with each other. It is a network protocol that helps data exchange between various systems—such as the engine, transmission, brakes, sensors, and more. CAN bus enables real-time, reliable, and robust communication, making it suitable for applications requiring extensive data coverage and integration between different machine components. The CAN specification allows for various protocol speeds to be implemented (with newer vehicles typically implementing the faster versions of the protocol).
OBD (On-Board Diagnostics)
OBD—specifically OBD-II—is a federally mandated and standardized diagnostic system used in most vehicles sold in the US since the mid-1990s. It provides a standardized way for diagnostic equipment to access and retrieve information from the vehicle's ECUs. OBD-II primarily focuses on diagnostic functions and provides access to a subset of data related to emissions, engine performance, and vehicle sensors. It is commonly used for emissions testing, vehicle diagnostics, retrieving fault codes, and connecting third-party devices such as GPS locators and dash cameras.
JBUS (J1939)
JBUS—also known as J1939—is a specific application layer protocol, and interface definition standard, that runs on top of the CAN bus physical layer. It is primarily used in heavy-duty commercial vehicles, such as trucks, buses, and construction equipment. J1939 defines a standard set of messages and parameter definitions for communication between ECUs in these vehicles. It allows for standardized data exchange related to vehicle control, diagnostics, and monitoring. J1939 is designed to meet the specific requirements of the heavy-duty vehicle industry.
In other words, CAN bus is the underlying network protocol used for communication between various machine systems. To simplify:
- OBD-II specifies the interface and protocols used for diagnostics and emissions-related purposes and is mainly used in passenger vehicles and light trucks.
- J1939 is an application layer protocol, and interface definition, specific to heavy-duty commercial vehicles.
- CAN is the underlying network used to allow various systems within vehicles and equipment to communicate with each other.
What are the benefits of using CAN?
When it comes to equipment and fleet management, CAN bus offers several benefits.
Data Coverage
CAN bus provides access to a wide range of data. It enables the collection of real-time information from various vehicle systems, such as the engine, transmission, brakes, sensors, and more. This extensive data coverage allows for a more detailed analysis of performance, fuel consumption, driver behavior, and other relevant metrics. CAN bus trackers can retrieve data beyond standard OBD-II parameters, including specific vehicle manufacturer data and advanced diagnostics.
Granularity
CAN bus offers a higher level of granularity in terms of data resolution. It provides access to individual sensor readings and system parameters if these are provided by the vehicle OEM (original equipment manufacturers) over the CAN bus, allowing for a more precise understanding of the asset’s behavior. This level of detail is particularly valuable for fleet managers who require accurate and specific data to optimize operations and identify potential issues.
Customization and Flexibility
CAN bus supports various data types, including numeric, text, and status information. It also allows for prioritization of messages, enabling critical data to be transmitted with higher precedence. CAN bus allows for the collection of a wide range of data points related to performance, maintenance, fuel, idle, and other mission-critical needs. This robust set of data allows your asset management team to be more proactive and have greater information for decision-making purposes, speeding up your time to repair and ultimately maximizing the uptime on your equipment.
Scalability
CAN bus is designed to support many interconnected devices thanks to its networked topology. CAN bus supports multi-node communication, allowing for easy expansion of the network by adding new nodes or devices. It follows a distributed architecture, where each node can send and receive messages independently.
Simplicity and Ease of Use
The CAN bus protocol is relatively simple compared to other network protocols. Its message-based communication model, with standardized message frames, facilitates easy integration and interoperability between different devices and systems.
Reliability
CAN bus is a robust and reliable communication protocol widely used in the automotive industry. It operates on a dedicated bus, separate from other vehicle systems, ensuring data integrity and minimizing interference. CAN bus is designed to operate in harsh and noisy environments. It uses a differential signaling scheme, which ensures reliable data transmission even in the presence of electromagnetic interference (EMI) and other disturbances. This reliability is crucial for fleet tracking, as accurate and consistent data is essential for making informed decisions and optimizing fleet operations.
So, CAN bus can be used for vehicles and equipment? The short answer is yes. While it is most associated with automotive systems, CAN bus is a versatile communication protocol suitable for several types of equipment and fleet needs.
CAN bus is widely adopted in automotive applications, industrial automation, and other domains. This widespread usage results in a broad range of compatible devices, tools, and software available in the market, making it easier to design and implement CAN-based systems.
These benefits have made CAN bus a popular choice for applications that require reliable, real-time communication, such as automotive electronics, industrial control systems, and more.
Which should you choose?
Any of the protocols described in this article can add value to your equipment and fleet management programs. The key is to find the solution that best fits your goals. Be sure to work with your equipment managers, maintenance personnel, and your solution provider to review your assets’ make/model/year. This will ensure the best protocol and connection point are selected.
In addition to CAN bus, there are also various methods of collecting run-time, location, and utilization data that may fit your organizational needs without the consumption and use of a total CAN bus solution. When in doubt, your IoT provider should be able to help you analyze your needs and assets and construct the best solution—and the best outcomes.
About Sunil Puranik
Sunil is a Technical Product Manager at Tenna dedicated to driving positive change in the construction industry. As one of the first engineers at Tenna, he witnessed the challenges faced by construction professionals, fueling his passion to develop innovative solutions. Leveraging his technical expertise, Sunil tailors Tenna's offerings to address industry needs, empowering construction companies to streamline operations and enhance productivity. Through active engagement with the construction community and a focus on staying at the forefront of innovation, Sunil is committed to making a lasting impact and helping construction professionals succeed in a dynamic landscape.