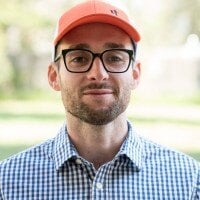
Managing construction equipment across various job sites is no small feat. With high-value assets constantly moving between locations, construction companies face challenges related to visibility, utilization, security, and maintenance. GPS tracking for construction equipment is an indispensable solution to these challenges.
In this blog, we’ll dive into what GPS tracking for construction equipment entails, why it’s essential for the industry, what features to look for, how to evaluate providers, and which solutions stand out in the market—along with why Tenna leads the pack.
What is GPS Tracking for Construction?
GPS tracking is the process of using the Global Positioning System (GPS)—a network of satellites that transmit location data—to track the position of an object in real time.
Hardware devices that leverage GPS can find the exact location of the item they are affixed to. These devices are classified as telematics trackers and can send this information to a central system using a cellular or satellite network for review and interpretation. For construction companies, this means they can track heavy machinery, vehicles, tools, and other important equipment anytime and anywhere with GPS trackers to identify the location of tracked assets in their fleet.
Why is GPS Tracking Essential for Construction Equipment?
Managing fleets of equipment without GPS tracking is like flying blind. GPS gives contractors clear insights, control, and smart tools for managing their fleet, which helps them make better decisions based on data, not just guesswork.
Here's why GPS tracking for equipment management is essential.
Read how Shoring Engineers saved between $50,000 and $120,000 with GPS tracking for its construction equipment.
Real Time Location Tracking
Construction equipment is frequently moved between sites, making it hard to keep tabs on where everything is. Real-time GPS tracking allows you to instantly locate any asset from your tracking platform app. This is especially helpful in large or sprawling job sites or when teams use equipment across multiple locations.
Plus, by working with a provider that offers geofencing, contractors can set site boundaries on a map to monitor exit and entry events based on GPS tracking equipment.
With GPS tracking, contractors can reduce equipment loss and theft. Reduced theft equals reduced cost of rentals, replacements, insurance premiums and more.
Read how Boudreau Pipeline saved $15,000 to $19,000 per month with visibility into their equipment data using utilization and idle reports from GPS trackers.
Optimized Equipment Utilization
A common challenge in construction is underutilized or idle equipment. GPS tracking systems that pull data from GPS plug-in units allow construction businesses to track usage patterns and identify which machines are being overworked and which are collecting dust.
Tenna’s platform includes utilization reports and dashboards to help contractors maximize utilization and ultimately ROI on their owned assets (and their telematics system purchase). With this data, businesses can find which machines are not used enough and redistribute resources more effectively across job sites so they can be assigned to new projects or job sites.
This helps reduce unnecessary costs, such as rental fees or paying to continue owning and operating equipment that isn't being used often.
Read how Viking Construction was able to update preventative maintenance activities based on usage and hours on machines with GPS equipment tracking.
Preventative Maintenance and Extended Lifespan
Maintenance isn’t just about reacting to breakdowns—it’s about preventing them. GPS tracking systems that work with GPS plug-in devices can analyze asset usage data that can warn contractors about service needs and misuse, such as extended idling. With Tenna, preventative maintenance triggers can be set and triggered based on usage hours or calendar days as appropriate for each asset type.
Additionally, GPS tracking devices can show problems found in equipment and vehicles. This includes fault codes and DTCs from the machine’s electronic control unit (ECU) or onboard diagnostic system (OBD).
Tenna’s solution includes automated maintenance tracking that extends asset life and reduces unexpected downtime.
Read how Rental Works processed more accurate customer bills for greater revenue with equipment utilization data from GPS tracking devices.
Job Costing, Billing & Accountability
Contractors bill for their equipment in a variety of ways, but regardless of what method is used, accurate billing requires accurate usage data. With GPS tracking, you can monitor how long each machine has been used (or located) at a job site. This can help with accurate job costing and client billing. It also fosters accountability among teams by providing an audit trail of equipment movement and use.
Key Features to look for in GPS Tracking Systems for Construction Businesses
When selecting a GPS tracking system for your construction business, it’s essential to consider the features that directly address construction industry needs. Here’s what to look for during the evaluation stage:
Real-Time Location Monitoring: Know where every asset is at any given time. Real-time updates help reduce loss, improve dispatching, and ensure compliance.
Geofencing and Alerts: Set virtual boundaries around job sites. Receive alerts when equipment enters or exits a site, helping reduce theft, monitor utilization, and enforce security protocols.
Maintenance and Utilization Analytics: Access reports on runtime hours, idling, usage trends, and maintenance history. This proactive approach keeps your fleet in optimal shape reduces downtime and helps improve resale value.
Integration with Existing Equipment Management Software: Look for systems that integrate with your current tech stack. Tenna, for example, connects with ERPs, accounting tools, and project management platforms. This creates a smooth data flow in your organization.
Top Options for GPS Tracking for Construction Equipment in 2025
Choosing the right GPS tracking solution for your construction business means evaluating key providers in the space. Here’s a quick competitive evaluation of some top options for GPS tracking for construction equipment:
Tenna |
Strengths |
Limitations |
Verizon Connect |
Strengths |
Limitations |
Teletrac Navman |
Strengths |
Limitations |
Samsara |
Strengths |
Limitations |
HCSS |
Strengths |
Limitations |
While general fleet tracking platforms offer solid GPS functionality, they often lack features built for the construction industry. Tenna is purpose-built for contractors, offering end-to-end asset management across mixed fleets, from heavy iron to hand tools.
How to Choose the Right GPS Tracking System for Your Fleet
Finding the best GPS tracking system for your construction company starts with evaluating your specific needs and growth plans.

- Fleet Size: Small fleets may need simple location tracking, while larger operations may require comprehensive solutions.
- Fleet Mix: Are you tracking only vehicles and heavy trucks, or also equipment assets, attachments, parts and tools?
- Tracking Goals: Do you need behavior tracking, fuel monitoring, or maintenance reminders?
- Tracking Frequency: Some operations require real-time updates, while others may only need periodic data.
- Ease of Use: A user-friendly interface is critical. Tenna’s intuitive platform ensures fleet managers, operators, and back-office staff can all work efficiently.
- Mobile Access: Choose a solution with mobile compatibility for field access.
- Integration: Can the system integrate with your existing ERPs or project management tools?
- Will the system grow with your fleet?
- Are there upgrade paths as your tracking needs evolve?
- Does the company have a roadmap for future technology advancements?
Tenna’s roadmap includes expanding analytics, AI-driven insights, and new tracking technologies—all tailored to the construction industry.
4. Assess Customer SupportResponsive, industry-specific support is vital. Tenna offers a dedicated customer success manager for larger fleets, ensuring smooth onboarding and ongoing value.
Why Tenna is the Leading GPS Tracking Solution for Construction
Tenna isn’t just another GPS tracking provider—it’s a construction-focused platform built from the ground up to serve contractors. Tenna offers:
- Mixed Fleet Tracking across heavy equipment, vehicles, tools, and materials
- Multiple Tracking Technologies (GPS, QR, Bluetooth) on a single platform
- Deep Construction Integrations with ERPs, accounting software, and scheduling tools
- Robust Reporting & Dashboards to drive data-based decision-making
- Unmatched Support with a team that understands the construction industry
If you're ready to optimize how you manage your fleet, reduce costs, and gain total visibility into your assets, schedule a demo with Tenna today.
By investing in GPS tracking for construction equipment, you're not just adding another layer of oversight—you're building a more efficient, cost-effective, and future-proof operation.
About James Glassman
James Glassman is a dynamic Regional Account Executive at Tenna, committed to delivering innovative technology solutions to the construction industry. As a key member of the Tenna team, James understands the challenges faced by today's contractors and is dedicated to helping them unlock the full potential of their construction operations. With a consultative approach and a passion for client success, James looks forward to solving contractor pain points and helping businesses streamline operations to drive growth.