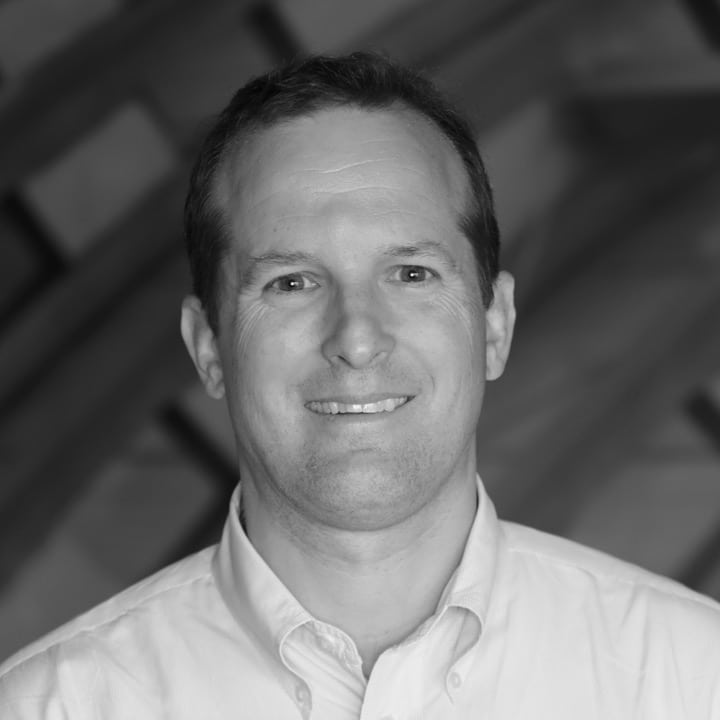
Although it was once on the cutting edge, we think of GPS and geolocation technology today as a part of everyday life. Our smartphones come with integrated GPS chips for navigation and websites frequently request our location to provide additional services. Multiple industries take full advantage of these tools to improve work efficiency, including the construction industry. GPS equipment tracking is the core element of today’s construction telematics solutions, fulfilling multiple roles and solving many problems.
Why Construction Companies Take Advantage of GPS Tracking for Equipment
1. Company GPS Tracking Systems Are Essential for Asset Management
As a contractor, one of your primary day-to-day challenges is asset management. While you can employ many strategies and approaches to manage your equipment more efficiently, none of them function if you don’t have visibility, as GPS tracking is at the root of an asset management system.
Asset visibility requires answering a simple question: Where is my equipment at the moment?
Previously, if a construction company wanted to know the location of all their equipment, they had to rely on making phone calls to each possible work site and collating the information manually. Any method without automation remains an imperfect way of tracking equipment, and even the smallest construction companies struggle with tracking can’t keep track of each of their tools and all their equipment.
Modern asset management solutions typically involve telematics software, and the core of all telematics is equipment GPS tracking.
Switching to GPS tracking for fleet and equipment management presents numerous advantages over methods of the past. The most significant benefit is connectivity to applications compatible with commonly owned devices such as smartphones and smart tablets.
After installing GPS tracking tags or activating integrated equipment GPS trackers on your assets, you can connect them with your asset management application and display the location of all connected equipment in real-time. There’s no better solution for asset visibility than knowing exactly where every asset is at any given moment.
Another significant advantage is adaptability. Quality fleet tracking GPS systems work on all kinds of equipment. You can install wireless GPS tracking devices on both your owned and rented equipment, allowing you to keep track of all assets, with flexible options to even track those your company doesn’t own.
You can even use GPS equipment trackers on assets other than typical construction vehicles. The best equipment GPS tracker suites let you track and thoroughly manage all of your equipment fleet resources through a mixture of mini GPS trackers, GPS tracking for trucks and vehicles, GPS trackers for generators and other non-moving equipment, and more.
2. Tracking Equipment with GPS Helps Prevent Theft
One of the most common yet critical risk factors in the construction industry is the threat of equipment theft, as construction vehicles and equipment are high-value assets. Every year, the construction sector in the United States loses up to $1 billion in stolen equipment, with a recovery rate of only 20%. Foreign contractors experience similar numbers, proving that construction equipment theft is a worldwide phenomenon.
European contractors lose approximately €1.5 billion every year to construction equipment theft, with a recovery rate of only 5% to 20% (3 to 10 times less than the stolen passenger car recovery rate). In the United States, one of the primary reasons behind this phenomenon is the much lower security compared to passenger cars. Flagship equipment like dozers and loaders can cost up to $200,000 but is easier to steal than a car of equivalent value. Additionally, most construction equipment counts as off-road vehicles, which means they require no registration. As a result, reselling stolen assets carries fewer risks for criminals.
Consequently, it falls on contractors to keep track of their equipment at all times. Implementing GPS asset tracking systems and anti-tamper GPS equipment tracker devices are one of the first steps of construction theft prevention.
Although GPS asset trackers can increase asset visibility and display the location of all registered equipment on a map, the best construction equipment GPS tracking devices can do more. One of the best ways to protect your assets from theft is to use GPS fleet trackers in conjunction with a geofencing system.
For example, you can set a geofence around an ongoing construction site, an equipment yard, or other property and areas your company owns. Whenever one of your assets enters and leaves a geofenced zone, the onboard GPS tracking equipment detects the activity and triggers the platform to send a push notification to managers and equipment operators.
Managers can then verify that their assets are traveling as authorized and moving as expected. This helps detect unauthorized use early enough to prevent equipment loss or, if needed, notify local law enforcement of a theft in progress.
3. GPS Asset Tracking Promotes Worker Safety
Although the most common application for enterprise GPS tracking systems is to improve asset visibility and facilitate equipment management, you can also use them to protect your employees.
Workplace safety is more critical than ever before in the construction industry. Despite that, statistics compiled by OSHA and the BLS revealed that in 2019 approximately 1 in 5 worker fatalities nationwide came from the construction industry, totaling 1,061 incidents.
Asset tracking via GPS can improve worker safety and reduce the number of injuries and fatalities in many innovative ways. For instance, fleet GPS systems integrated into company vehicles can communicate with onboard telemetry equipment and detect driver behavior patterns and coaching can be provided for drivers that repeatedly exceed the speed limit, for example, promoting safer driving.
These GPS tracking solutions are invaluable for detecting what the industry refers to as high-risk drivers. Using GPS data to identify high-risk drivers early allows you to provide them with the necessary re-training or other corrective behaviors before they are involved in a costly accident.
4. Asset Trackers and GPS Monitoring Can Help You Save Money
GPS tracking systems can, as part of a complete telematics system, help you reduce expenses and increase profitability in four ways:
-
-
- Encouraging efficient equipment operation and improving fuel economy
- Monitoring asset utilization rates
- Logging geographic data to take advantage of fuel tax refunds
- Integrating with map software and traffic monitoring solutions for efficient routing
-
How Equipment Trackers and GPS Solutions Improve Fuel Economy
We already covered how a construction GPS tracking system can help promote safer driving and prevent your workers from breaking road safety laws and regulations. But did you know the same systems can also help you further improve your workers’ driving and promote careful, fuel-efficient driving?
GPS tracking systems can assist or supplement onboard telemetry and calculate each asset’s average fuel consumption rates. This data can, in turn, help you determine driving habits and help you correct inefficient driving behavior (e.g., unnecessarily hard accelerations or braking).
How GPS Tracking Can Improve Maintenance Routines
GPS trackers can supplement telematics data with location-based information and capture equipment utilization. The data provided includes detailed information about your assets, such as engine hours/miles, service hours, uptime by set periods (day, week, month, lifetime), and more.
This information can help you improve the efficiency of your maintenance routines and optimize your preventive maintenance schedules. It can also help you maintain your vehicles’ and equipment health at optimal levels.
Taking Advantage of Fuel Tax Refunds with GPS Data
One of the most significant types of recurring costs of owning and operating heavy equipment is fuel costs. Most equipment on a construction site functions on gasoline or diesel fuel, making it essential to trim fuel costs as much as possible. While promoting better fuel efficiency is one of the most common ways to save money on fuel, there is a lesser-known alternative. You can use federal and state tax refunds.
According to the Internal Revenue Code (26 U.S. Code paragraph 6421), the federal government and most state governments tax gasoline and diesel fuel for the explicit purpose of road and highway maintenance. Federal fuel tax funds go toward the interstate highway system, whereas state contributions fund other roads.
However, the law distinguishes between fuel usage on government-managed roads and the fuel used for off-road applications. This includes personal use (on private property), farming, or construction equipment.
The best GPS trackers for equipment management can help you monitor how much time and fuel your equipment has burned while off-road by combining location data with detailed fuel consumption logs. This information can help you prove your off-road fuel usage when filling out the requisite forms.
If you wish to benefit from a federal fuel tax credit, you can file a Tax Return Form 4136, Credit for Federal Tax Paid on Fuels. For your local state’s equivalent, check your local laws. You can supply telemetry logs and GPS data records alongside your form to support your claims.
Note that not all states offer refunds, and the tax rates vary by state and fuel type. For example, if you operate in Arizona, you must pay $0.19 per gallon of gasoline and $0.27 per gallon of diesel in taxes.
5. GPS Vehicle Management Enables Data-Driven Accountability
GPS asset tracking systems place undeniable emphasis on worker safety and promote better and more efficient worker habits. You can also take advantage of these systems to protect your workers from disputes and litigations.
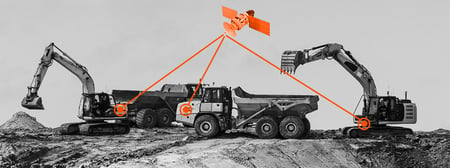
Use GPS equipment tracking systems in conjunction with driver safety devices (like GPS-enabled dash cams) to hold your drivers to a higher standard of accountability. Back your company’s claims to insurance companies or in a court of law using hard data.
If one of your workers is involved in an accident while using a company asset, GPS-connected safety devices can help you provide actionable evidence to back your claims. These tools are invaluable for resolving insurance claims more quickly or combating staged accidents, a form of insurance fraud.
If incorporated into your equipment management platform, you can also present dash cam footage and GPS location logs as evidence that your worker respected speed limits and did not break road safety rules. Resolving legal claims more quickly means spending less on legal fees and preventing your insurance premiums from rising in the long term.
Protect Your Construction Site With Equipment GPS Trackers
The construction industry is one of the fastest-growing sectors for GPS tracking device adoption, and once you realize all of the system’s benefits, it’s easy to see why. GPS asset tracking systems are more than just a way to put your equipment on a map. They are a multi-faceted tool that facilitates asset management in every possible way, helping your company improve overall work quality, safety, and cost-efficiency.
Tenna has the solutions you need. Book a demo today and discover how modern GPS tracking systems have revolutionized equipment fleet management.
About Mark Facciani
Mark’s expertise is in building and leading teams. Formerly a middle school teacher, team leader, and wrestling coach for 15 years, Mark has spent the past 5+ years at Tenna growing key departments including marketing, customer success, and sales. Today, as VP of Sales Development, Mark leads the team that spearheads outreach efforts, helping Tenna meet tomorrow’s future customers.