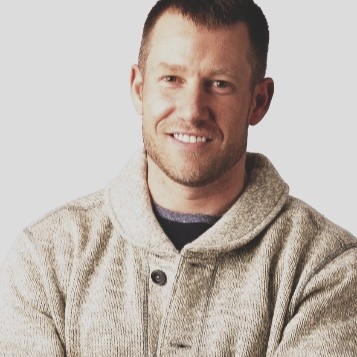
Between high material costs and increasing labor shortages, keeping a construction project on time and within budget has never been more difficult. Therefore, it’s crucial that all equipment purchases make a positive impact on the bottom line.
TCO is commonly understood to be the cost associated with purchasing a piece of equipment, utilizing that equipment and conducting planned maintenance for it. The true total cost of any business equipment, however, and particularly in the construction industry, can only be estimated following constant analysis of usage statistics, age, maintenance needs and more. It’s important to understand the total cost of ownership (TCO) for all equipment when making business decisions relating to its purchase, lease or sale to understand ROI and make better, more informed investments in the future.
How to Calculate TCO
TCO is calculated in different ways depending on the expense considerations of each contractor. Typically, TCO calculations include how much it costs to acquire a machine, the expenses incurred during regular and unplanned maintenance, and the profits generated directly from the use of the machine. However, there will always be unique expense considerations for individual contractors based on their use cases. All of these factors should be considered to achieve a true understanding of the financial impact a piece of equipment has on a business's bottom line.
5 Ways Modern Equipment Management Software Can Help Construction Businesses Reduce the Tco of Their Equipment
Minimize Equipment Idling Time to Ensure It Is Used Efficiently Between Maintenance Intervals
Heavy equipment can be exceedingly expensive. Business leaders who invest in equipment expect to generate as much value as they can out of their machines. However, the reality of construction is starkly different. It’s second nature for construction operators and drivers to idle equipment and trucks for long periods of time. Industry research revealed that approximately 40% of a machine’s time is spent running—but not in use. This can cause technical issues that force faster service needs, further downtime during maintenance and repair as well as unnecessarily burn fuel which equals money.
Fully featured equipment management systems can alert managers when business-critical machines are running but are not producing the output expected from that time period. This information can help businesses reduce costs down the line and help them make the most of their equipment.
Learn About the Utilization Levels of Your Most Expensive Equipment
Understanding the costs associated with construction equipment goes beyond the costs related to a single asset. Construction businesses are constantly looking for specialized tools and equipment they can rent for a few days for certain tasks. However, construction equipment is versatile and there may be another option within the fleet that could do the job without the need for additional equipment.
Understanding what is available within a company’s mixed fleet of assets along with knowing how equipment can be used can prevent further expenses in unnecessary equipment rentals or additional manpower. Fully integrated software can help you find additional areas where owned equipment can be utilized to maximize productivity and output.
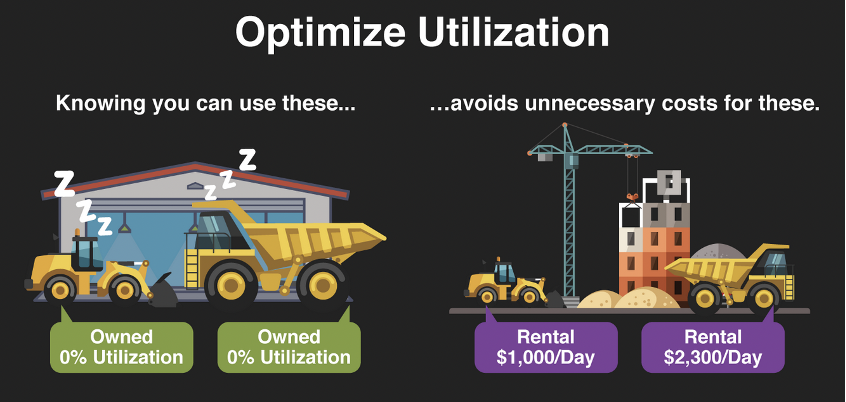
Conduct Preventative Maintenance to Reduce Unplanned Downtime and Excessive Repair Costs
Maintenance is an integral part of owning and operating specialized equipment. There are two approaches that business leaders take to conducting this maintenance; reactive and proactive. A reactive approach involves responding to calls from the field that there is an issue with a piece of equipment which creates a fire drill and can bring project operations to a halt. The cost impact to the project along with the inefficient use of the equipment manager, mechanics and others’ time adds up quickly.
This improper maintenance can lead to significant costs for business leaders, costing up to $4.5 million between parts, supplies, labor, and specialty repairs. Modern equipment management software can help construction leaders get ahead of these issues by proactively prompting preventive maintenance intervals based on the actual hours/mileage currently on the asset and alerting managers to technical problems so they can solve issues before they disrupt daily operations.
Use Intelligent Software to Find the Most Productive Settings for Specialized Equipment
Human behavior is a variable that many construction owners fail to account for when analyzing equipment performance. However, the people that operate the machines have a direct impact on how well a piece of equipment performs on the ground.
Technology can help provide business leaders with insight on how their ground-level staff are utilizing new and existing equipment. Artificial intelligence, for example, can also help business leaders identify the optimal settings for existing equipment to provide maximum output with the way staff are using the equipment.
Understand the True Cost Difference Between Buying and Renting Assets
As supply chain delays continue to make procuring new assets challenging and expensive, more business leaders are turning to rented or used equipment to minimize business disruption and reduce costs. However, rented or used equipment with a lower cost of entry can sometimes become more expensive in the long run than buying new assets.
Business leaders should consider that used equipment usually requires more maintenance and repairs than new equipment and has much less extensive warranty coverage. Understanding the difference in the total cost of buying and renting equipment can help project leaders make informed financial decisions relating to their most important machines.
Ultimately, construction equipment represents one of the most substantial costs a business leader has to consider. This is true even for rented equipment with a seemingly straightforward cost to the company. Business leaders must stay on top of expected and unexpected costs that can add up over time.
Intelligent software can help businesses avoid human error, reduce time lags, and consolidate information that would otherwise be spread over disparate business departments. Equipment management software allows businesses to consolidate TCO calculation with fleet management, equipment tracking, and predictive maintenance, among other important features. Construction companies rely on business-critical equipment and must understand what it takes to keep it running at optimal capacity.
Contact Tenna to learn more about calculating the total cost of ownership of your mixed fleet assets.
About Tom Stemm
Tom Stemm is the CEO/Founder of Ryvit, a partner of Tenna’s. He was inspired to build Ryvit when several of his clients in the construction industry had asked for some custom integration development work. At the time, Tom was part of the founding team at GadellNet (a fast-growing IT consulting firm in St. Louis, MO), and they realized that there was a significant gap in the construction tech industry – namely that, while tech purchases were high, the adoption rate of those solutions throughout all stakeholders was still lagging. After a very diligent launch process, Ryvit was born to address the rampant problem of a disintegrated tech stack in the construction technology space. Tom continues to lead a team of integration developers, application enthusiasts, customer heroes, and sales superstars on a mission to eliminate duplicate data entry and rampant data errors from the construction technology world.