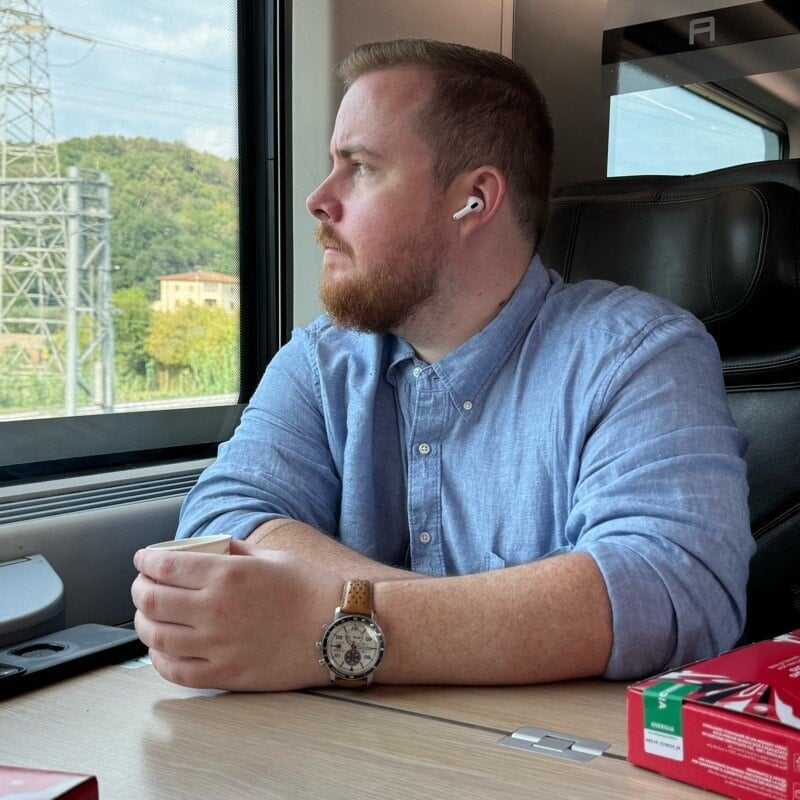
In the construction industry, equipment downtime doesn’t just disrupt workflows—it costs time and money. With every minute of unexpected downtime, project delays increase, teams underutilize labor, and profit margins shrink.
The good news? You can avoid these costly setbacks with equipment maintenance software designed specifically for construction businesses. In this post, we’ll explore how a well-executed preventative maintenance schedule helps streamline maintenance operations, cut costs, and keep your equipment running smoothly and safely.
What is a Preventative Maintenance Schedule and Why Does It Matter?
A preventative maintenance schedule is a proactive plan that involves performing routine inspections, servicing, and repairs on equipment before failures occur. Unlike reactive maintenance, which kicks in only after breakdowns happen, preventative maintenance helps you stay ahead of costly surprises.
Why Preventative Maintenance Software is Critical for Construction Companies:
- Financial Impact: Predictive maintenance can significantly enhance efficiency in construction projects by reducing equipment downtime by up to 30% and lowering maintenance costs by 20%.
- Cost Efficiency: Reactive maintenance can cost up to three times more than planned servicing due to emergency repairs and extended downtime.
- Safety & Compliance: Regular maintenance ensures equipment runs safely, minimizing risk and avoiding costly compliance violations.
How Equipment Maintenance Software Optimizes Preventative Maintenance Schedules
Preventative maintenance software plays a key role in managing and automating maintenance schedules. Here’s how the right solution can transform your maintenance operations:
Use Telematics to Drive Smarter Scheduling
Telematics technology tracks equipment usage, performance, and health in real time. By integrating telematics into your equipment maintenance software, you can:
-
- Monitor Accurately: Schedule maintenance based on real machine data, not arbitrary dates.
- Predict Failures: Spot issues early through performance trends and alerts.
- Improve Reliability: Reduce unplanned repairs with condition-based scheduling.
Automate Alerts and Work Orders
Top-tier preventative maintenance software automates service reminders and creates work orders without manual input. This ensures:
-
- Timely Maintenance: Equipment gets serviced right when it needs it—no more guesswork.
- Streamlined Workflow: Reduce administrative tasks and eliminate oversights with automated processes.
Centralize Maintenance with Equipment Management Software
An integrated platform that combines equipment maintenance with full equipment management offers unmatched efficiency. Benefits include:
-
- Unified Data: Access all maintenance records, service intervals, equipment inspections and usage metrics from one dashboard.
- Team Collaboration: Make sure everyone—from field crews to fleet managers—aligns with equipment status and service plans.
- Connection to Parts Inventory: Request parts and efficiently schedule preventative maintenance without inventory issues that cause project delays.
Leading Preventative Maintenance Software Options
When evaluating preventative maintenance software for your construction business, it’s important to compare solutions based on features and functionality, industry fit, and integration capabilities. Here's how some of the leading platforms stack up:
Tenna |
Tenna is purpose-built for the construction industry, offering a comprehensive equipment management platform with robust preventative maintenance features. It combines real-time telematics, automated preventative maintenance scheduling, digital work orders, inspections, and centralized service history tracking in one unified system. Tenna stands out by providing visibility and connection for field, shop, and office teams. This helps contractors make maintenance workflows easier and improve uptime. Construction businesses appreciate that Tenna’s solution is not a one-size-fits-all CMMS but a platform engineered specifically for mixed construction fleets. It seamlessly integrates maintenance tasks with equipment tracking, inspections, safety and compliance, utilization, and overall asset management. |
HCSS Equipment360 |
HCSS e360 is a well-established maintenance management tool designed for heavy construction companies. It focuses on shop-level maintenance workflows, including work order generation, parts inventory tracking, labor timecards, and preventive maintenance scheduling. Many contractors rely on HCSS e360 to organize and document their equipment servicing routines, especially if they already use HCSS’s suite of project management tools. While powerful in the shop, HCSS e360 can require additional tools or integrations to provide full visibility into field equipment usage and telematics data. Real-time condition monitoring may depend on third-party systems, and syncing information across departments can be more manual if not fully integrated with other platforms. |
Fleetio |
Fleetio provides maintenance tracking tools for mixed fleets and general asset management. It supports service reminders, work order creation, and digital maintenance logs. Fleetio has strong mobile features and many third-party integrations. This makes it flexible for companies that manage vehicles and equipment. However, it is not built exclusively for the construction industry and may require customization or add-ons to handle the unique demands of large-scale construction operations. |
UpKeep |
UpKeep is a CMMS geared toward general maintenance and facilities management. It includes scheduling for preventative maintenance and tracking work orders. However, it has limited telematics integration. This product may not suit heavy equipment or mobile construction settings. It works well for internal assets and light industrial uses. However, construction companies may find it lacks the features needed to manage complex equipment fleets. |
ManagerPlus |
ManagerPlus serves a variety of industries and offers customizable maintenance workflows, inspection management, and reporting features. It supports preventative maintenance and integrates with telematics providers. However, because it's designed as a broader enterprise asset management system, it may be more complex to configure and maintain for construction-specific use cases. The user experience can vary depending on setup and integration needs. |
Why Contractors Choose Tenna
While many of these platforms offer solid preventative maintenance schedule capabilities, Tenna differentiates itself by addressing the real-world challenges construction contractors face daily:
➡️ Read more about why Tenna is the best construction equipment maintenance software option to streamline preventative maintenance schedules for your fleet.
-
- Built for Construction: Every product element—from telematics to work order automation—is tailored for mixed equipment fleets, jobsite conditions, and contractor workflows.
- All-in-One Platform: Maintenance is not siloed; it’s natively integrated with asset tracking, inspections, utilization data, and project-level visibility.
- Real-Time Field Connectivity: Field crews and mechanics stay informed with instant access to equipment status, service history, and upcoming maintenance needs.
- Proven ROI: Contractors have seen measurable reductions in downtime and maintenance costs using Tenna’s preventative maintenance solution.
Case Study: How Zefiro Cut Downtime with Preventative Maintenance Schedules Using Tenna
Company: Zefiro, a leading infrastructure and demolition contractor Challenge: Manual maintenance tracking led to unplanned breakdowns, high repair costs, and project delays. Solution: Zefiro adopted Tenna’s equipment management platform, integrating:
|
Results:
|
|
By going from reactive to proactive maintenance, Zefiro significantly ⬇️ lowered costs and ⬆️ boosted operational efficiency.
Take Control of Your Preventative Maintenance Schedule
If you still use spreadsheets, whiteboards, or reactive servicing, it’s time to upgrade. Otherwise, you might fall behind your competition. Preventative maintenance software empowers construction businesses to:
- Minimize downtime
- Extend equipment life
- Lower operating costs
- Boost safety and compliance
Next Steps:
- Evaluate Your Current Maintenance Process
- Adopt a Robust Equipment Maintenance Software (like Tenna)
- Automate Preventative Maintenance Schedules
- Train Your Team on Best Practices
Want to eliminate downtime and keep your fleet on schedule? Explore how Tenna’s preventative maintenance software can help you take full control of your equipment operations.
About Parker Van Winkle
Parker is a seasoned Customer Account Manager at Tenna with a passion for building strategic partnerships. He excels at understanding contractors' needs and translates those needs into real results. With a keen eye for identifying opportunities for growth and efficiency in the construction industry, Parker proactively monitors KPIs and guides customers toward achieving their goals. His approach is rooted in trust and a commitment to delivering exceptional value.