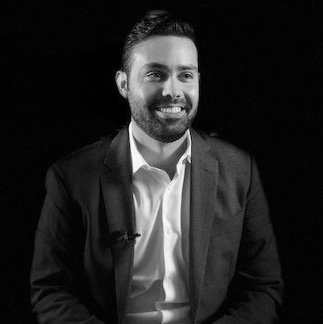
Humans have been tracking their equipment for thousands of years. In the past, it was quite simple. Count how many sheep or goats you have and write it down – starting with clay tablets or papyrus and then advancing to paper.
Over time, writing materials became easier to use. The basic count-and-write approach remained unchanged until the latter part of the 20th century, when tracking technologies became more sophisticated.
The first big breakthrough came in the mid-1980’s, with the introduction of personal computers and spreadsheet software. Spreadsheets made it easier to update inventory counts and to instantly share the tallied information with others. Yet, they didn’t offer other helpful features, such as historical tracking; they lacked real-time tracking capabilities. The data became dated as soon as someone entered it into the spreadsheet.
Stepping Up the Game with Wi-Fi
Around 2005, someone got the idea of attaching Wi-Fi tags to equipment and other mobile assets as a means of tracking their locations. The tags “chirped” every few seconds to signal their location, and this information would get recorded in a database. The Wi-Fi approach enjoyed a brief period of popularity, but three flaws prevented broad adoption among commercial enterprises.
The short battery life required frequent replacement, a time-consuming process for companies with assets spread over a wide geographic area. The Wi-Fi tags came with a hefty price. And the Wi-Fi approach worked well inside warehouses and buildings with a local area network, but had no practical application for tracking assets in the field.
Active vs. Passive Equipment Tracking
As equipment tracking technologies continued to improve, two tracking options became available – passive and active. Their use depends on what you’re tracking and why.
Active tracking provides continuous information about equipment without needing human assistance. For example, a GPS tracker can automatically map and transmit the route taken by a truck driver, including the speed and direction of the truck. A GPS tag on heavy machinery at a construction work site can do the same. Active tracking offers the advantage of having the equipment track itself.
With passive tracking, the tracking device does not send out regular reports about the location and status of the equipment. Instead, the information is tracked and recorded only when you need it. The driver must visit the location of each asset, scan the label or tag with a smart phone or reader, and wirelessly relay the data to the home office.
Passive tracking is ideal for companies that only need to update equipment information when something changes, such as moving it to a new location or renting it to a different customer. Passive tracking can be used with almost any type of asset, including very small ones, and it typically costs less than active tracking systems.
QR Tracking: Current State of the Barcode Art
Once companies that need to track a lot of assets began to fully understand the potential of passive tracking, they began adapting the technology to their own needs.
Initially, companies began placing simple, one-dimensional barcode labels on their assets in the field, and retrieved the information using hand-held barcode scanners. Although simple and easy to use, one-dimensional barcodes quickly fell out of favor because they could only hold limited amounts of information. Plus, the need to buy barcode scanners added to the system’s cost.
The latest advance in equipment tracking technology, and one of the technologies we use at Tenna, is QR (quick response) tags. Invented in 1994 by a Toyota subsidiary, QR tags have been around more than two decades. However, the technology didn’t start gaining wide acceptance until about five years ago.
What makes QR different and better than other barcoding technologies?
The one-dimensional barcodes used on most consumer products are read by bouncing a narrow beam of light onto the code. The scanner then interprets the data by analyzing the pattern of light reflected off the white gaps between the dark lines. In contrast, two-dimensional QR tags are scanned using smart phones or other mobile devices. The devices read the black and white squares with their image sensor, and then interpret the data using their system processor. The scanned data is then stored on the device or instantly sent to the office.
A QR tag can hold up to 100 times more information than a one-dimensional barcode, enabling you to retrieve a wide variety of data about your equipment.
QR tags don’t require a special reader to scan them; drivers can use their own cell phones or mobile tablets. Plus, Tenna’s metallic tags have a good track record of standing up to severe weather conditions for many years, making them more cost-effective over the long run.
Perhaps most important, QR scanning gives you real-time information about your field assets. As soon as the driver scans a piece of equipment, the data is automatically sent to your software database, which immediately updates the new information. As a result, you always know the precise location and status of every piece of equipment, which enables more efficient use of your entire fleet.
Going Beyond Barcoding
At Tenna, we understand that businesses have different asset tracking needs. That’s why we offer all the latest asset tracker technologies, so you can choose the one(s) that fit your business model and your tracking needs. Each of these technologies offers slightly different features, applications and advantages. Understanding their differences can help you select the right tracking technology, or combination of technologies for your asset tracking needs.
Our selection of asset tracking technologies includes:
• RFID. Radio frequency identification, or RFID, tracking systems consist of three separate components: an RFID tag (also known as a smart label), an RFID reader and an antenna. The tag contains an integrated circuit and the antenna. The antenna transmits data to the RFID reader, which acts like the scanner in a barcode system.
• Once the tags are attached to your equipment and tools, RFID offers several scanning options for collecting asset data. Using the handheld RFID reader, drivers can scan the tags from up to 100 feet away. You can also install fixed-mount RFID stations at a project site or next to the gates of your yards. The fixed mount approach makes RFID tags ideal for tracking equipment as it enters or exits your locations, allowing it to automatically track assets as they move past your antennas – without any human involvement.
• Bluetooth. Useful for tracking small tools and equipment, Bluetooth asset tags make it easy to track assets in short-range areas, without manual involvement. Depending on the “ping” interval and power output, batteries typically last one to three years. Scanning distance ranges from 40’ at low power to up 140’ at full power.
• Bluetooh Low Energy Trackers. Our BLE tracker solutions also include Bluetooth Low Energy (BLE) beacons. These send out regular “heartbeats” which can be received by a smartphone or by a Tenna GPS asset tracker, which automatically records the asset’s location and stores the data on Tenna.
• GPS. Perhaps the most versatile asset tracking tool, GPS provides asset location, navigation and timing services by using a transmitter to connect to a global navigation satellite system. GPS tracking can track assets anywhere they are located as long as you have a cellular signal. Plus, our battery-assisted units are especially useful for equipment that doesn’t have its own power source. GPS can also provide location, speed, fault codes and other vehicle diagnostic information by connecting to a vehicle’s electronics control unit. If you only need location data, GPS can be mounted without onboard diagnostics connection.
• LoRa (Long Range) Trackers. These long-range automatic GPS devices can track assets – even without cellular coverage – by enabling you to set up your own private IoT network at your own worksites. Here’s how: LoRa non-cellular asset trackers collect your asset data and send it to receiving units at your project site, which then connect to the Internet via Ethernet or Wi-Fi. (LoRa does require a cellular backhaul at each site, but only one, in order to upload your data to the Tenna database.) The typical range for a gateway is up to three square miles, but you can always add more gateways to extend the coverage range.
• Tenna RFID All-In-One Reader System. To maximize our RFID tag capabilities, Tenna developed our own stationary site-based RFID reader. With a range of up to 180 feet (for signals sent from battery-assisted RFID tags) the system lets you track vehicles, tools and equipment as they enter and exit your work sites. The system automatically reads the RFID tags and transmits the data to your Tenna system, providing real-time tracking and inventory without operator involvement.
With these asset tracking technologies, you can efficiently and cost-effectively manage everything across your fleet, work sites, customer locations, yards and inventory. You can track assets automatically or manually. You can track short- or long-range. You can track using your own smart phones or tablets, even in areas that don’t receive cellular coverage.
Regardless of which technology you choose, you get a powerful asset management tool that helps to maintain accurate inventory counts, improve productivity, enhance customer service and add more dollars to your bottom line.
We’ve come a long way from tracking sheep on clay tablets! With Tenna and the ability to customize your tracking needs, you are keeping your asset management ahead of the curve.
About Austin Conti
As CEO and Co-Founder of Tenna, Austin leverages his international experience in construction operations for civil, building, and energy projects with The Conti Group, which has built successful, reputable businesses that make a positive impact on the world in construction, engineering, renewable energy, real estate, technology, and biotech. His passion for entrepreneurship led him to create a construction technology platform built on over a century’s experience from The Conti Group.