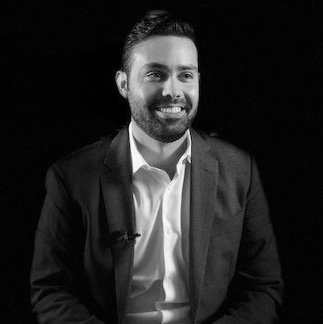
Completing projects on time and within budget is a complex, challenging endeavor, especially if your business has several concurrent jobs spread over a broad geographic area. Asset tracking is a critical tool to helping teams control their assets. However, there is more to asset management than just tracking. Asset management is a comprehensive process that includes asset tracking.
Smart managers reduce the complexity and get more work done in less time by using a digital asset management system. Here are three reasons why you should, too.
1. Managing daily workflow
Every day, large assets and material inventory items need to arrive at the right job sites on time, in the right amount, and with all associated parts and components. In the construction industries, workers need to have the correct tools and equipment on hand to perform highly specialized tasks such as moving earth, laying foundations, installing piping and cables, or drilling underground. A typical workflow on a construction site requires a coordination effort from many different places going in many different directions to get people, equipment, materials and resources where they need to be in a timely manner.
At the end of the day, managers want to make sure tools and equipment that travel from job to job are returned to their assigned set and brought back to the yard when no longer needed or to the shop for routine maintenance.
Managers can streamline their daily workflow by utilizing a construction asset management system that helps them efficiently transfer assets from one job site to another, track asset performance in real time and make decisions to effectively deploy assets in response to conditions in the field as they occur. Asset management systems give managers visibility into where assets are at any time and gives them the ability to schedule their logistical movements of all company assets across locations.
2. Tracking asset activity and fleet performance in the field.
To facilitate this daily juggling act, managers need to know how their assets are performing in the field. Are engines run only as long as it takes to complete their tasks, or do they have excessive idling or downtime? Is equipment reported for maintenance when alerts or signs of wear-and-tear arise, or are they overworked to complete a task, inadvertently becoming damaged? Are the shortest and most efficient routes being utilized, or are extra miles being added on the vehicle? Are company safety policies and public laws being obeyed, or does speeding occur?
To efficiently manage assets, managers must have accurate data on equipment utilization, including how many hours an asset is needed onsite to perform a particular activity, or how many tools are needed amongst the crew to perform an activity together? Without this knowledge, planning for future jobs will be based more on guesswork than on solid data managers can rely on and rates are likely to be inflated.
For companies that manage fleet vehicle operations, managers are responsible for ensuring their vehicles follow US DOT regulations. Each trip for each driver and vehicle needs to be tracked and documented with an electronic logging device (ELD), with accurate reports on how much time is spent behind the wheel. Separately, drivers are required to complete daily driver vehicle inspection reports (DVIRs) to ensure their vehicles have been inspected for safety and full functionality before getting on the road.
Digital asset management systems allow managers to view telematics data that provide insights on utilization, maintenance, location, inspections, compliance and more to monitor operational performance.
3. Access to asset data in real-time for remote monitoring.
With remote asset management, managers can quickly access the data they need to resolve problems, facilitate and improve productivity, and optimize personnel and resource utilization. If a tool gets lost or misplaced, managers can review the asset tracking system to see who used (scanned) it last and where to help locate it. Having this data available for every tool in inventory eliminates the need to physically track down assets that may have gone missing or been left behind, wasting valuable time. Asset management systems give employees the tools view this data to optimize their time and improve their productivity.
Asset management provides a treasure trove of meaningful data that managers can use to make informed decisions to improve operations and safety. For example, they can track idling in attempt to conserve fuel and reduce associated operational costs. When using telematics tracking with onboard diagnostic capabilities, fleet managers can easily identify which vehicles burn the most fuel or have the most diagnostic trouble codes without needing to physically inspect the vehicle. This enables them to determine which models operate most efficiently and when it becomes more cost effective to trade in older models for newer ones.
They can also monitor key driver metrics such as speeding to hold drivers accountable for complying with company policies and promote safe driving.
With drivers dispersed across broad geographies, asset management provides both a big-picture view of what the entire fleet is doing at any given time and the ability to zero-in on a single vehicle to check its location and performance. With just a few clicks, managers can quickly see how far and wide their operations range visually and tell whether a particular vehicle has completed a trip or is still en-route.
Asset management allows managers to be effective by running reports, analyzing results for areas of improvement, affecting change where improvements are needed, and monitoring progress to help better their business, earn and save more, and impact a positive transformation.
Not convinced yet?
Perhaps the biggest advantage of asset management is having all the data organized and accessible on one integrated, easy-to-use platform. Total, comprehensive asset management allows you to connect your distinct asset types for management on a single system, which provides all-encompassing data on all your assets. This is most cost-effective and easier to control than managing them separately using different systems or providers.
No matter how widespread your job sites and asset deployment, asset management lets you see everything you own – including where it is and how it’s performing – all in one place.
By monitoring availability, engine hours, driver behavior, fleet maintenance, and location data, asset management provides a powerful tool for encouraging employees to work smarter and safer. The data can be used in many ways, such as promoting employee accountability for keeping track of assets and equipment in the field, or driver reward programs to incentivize employees to change unsafe driving habits into safe ones.
Asset management doesn’t just impact managers, but it also impacts employees of all levels which aids in the buy-in and adoption of the system for the solutions to work. An optimal system gives field-level employees the tools to enable solutions individually and as part of a whole to make their jobs easier. There are no downsides to investing in asset management!
Whether your business uses heavy yellow iron, on-road fleet vehicle, miscellaneous mid-size assets or only tools, you can benefit from making asset tracking an integral part of your management strategy. Tenna asset management puts you in control of your assets and provides operational insights to help managers drive improvements and affect change. Check out Tenna’s one platform equipment management solutions and Book a Demo today.
About Austin Conti
As CEO and Co-Founder of Tenna, Austin leverages his international experience in construction operations for civil, building, and energy projects with The Conti Group, which has built successful, reputable businesses that make a positive impact on the world in construction, engineering, renewable energy, real estate, technology, and biotech. His passion for entrepreneurship led him to create a construction technology platform built on over a century’s experience from The Conti Group.