
Changes to the modern landscape have forced businesses to revisit their construction equipment maintenance software and programs. The construction industry realizes that even a small deficiency in equipment maintenance will silently leak money and kill productivity. This article discusses the philosophies of maintenance, where construction teams go wrong, and the pillars of a strong construction equipment maintenance program.
In an age of supply chain troubles, worker shortages, and delayed repairs, construction companies have begun revamping their fleet maintenance programs. Overlooking maintenance leads to all sorts of costs – not just the cost of the repair. There is the cost of replacement, the lost time, the busted deadlines, and the feeling of uncertainty.
In the past, there were fewer methods of predicting when and how to maintain tools or heavy equipment. However, modern innovations have given construction teams technology that makes maintenance smarter, faster, and less expensive.
Equipment Fleet Maintenance: Three Maintenance Management Concepts
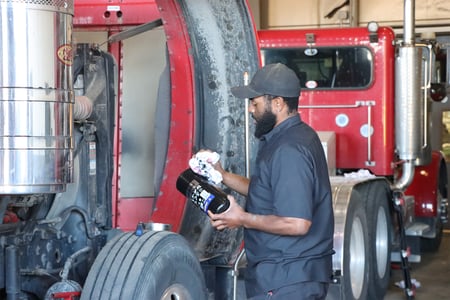
Let’s start by defining our terms: what is equipment maintenance management? Equipment maintenance is the scheduled or unscheduled repair or updates to any portable assets, including heavy equipment, mid-sized assets, and construction vehicles. Maintenance can be as simple as an oil change or inspection, or as complex as an engine rebuild.
However, not all construction equipment maintenance strategies are equal. There are many types and subcategories of equipment maintenance practices, but they all fall under three general categories:
- Reactive maintenance
- Preventative maintenance
- Predictive maintenance
The next sections expound upon these three philosophies.
Reactive Equipment Maintenance for Construction Equipment and Vehicles
With a reactive maintenance model, companies react to failed equipment. If the tire goes out, they replace it. If the axle breaks, they repair it. There may be some routine checks and repairs, but for the most part, the tool or vehicle is used until it begins to break, then repaired, and finally replaced.
Reactive maintenance is clearly not the most optimal route for construction teams, yet surprisingly, it’s still very common today. For very small businesses, reactive maintenance might work, but it certainly isn't the most efficient or sustainable method.
An unexpected trip to the dentist is a good analogy of reactive maintenance. Someone can either go to the dentist for a regular, relatively pain-free cleaning (preventative maintenance), or they can skip the routine cleanings and be forced to have cavities drilled or teeth pulled when they make an appointment after experiencing pain (reactive).
Let’s talk about preventative maintenance.
Preventative Maintenance for Construction Equipment
A preventative maintenance program for equipment seeks to maintain vehicles and smaller assets before they fail. For example, regularly changing the oil on a vehicle at recurring mileage intervals or bringing heavy equipment into the shop for routine engine service. Preventative maintenance is common, but not all forms of preventative maintenance are equal.
Suppose that five years ago a company purchases ten identical new vehicles. Half the vehicles performed heavy-duty work and half performed light-duty. The heavy-duty vehicles are beginning to wear out, and the company owner is contemplating replacements – should they just replace the entire fleet?
In some cases, the answer might be yes. But most people would point out that half the vehicles are still functional – indeed, these vehicles might have many more miles of strong service. However, teams can only know this if they have good data on each vehicle.
Just by having a close eye on the fleet of vehicles, they would know that half of them still have a long life ahead. An assessment of heavy equipment operating costs concluded that it’s more important to look at hours (or miles as applicable) used than years of service when calculating maintenance and replacement routines.
The preventative system is a good maintenance model. But good preventative maintenance doesn’t just look at the expiration dates on the packaging, good preventative maintenance looks at the entire “story” behind equipment use.
In fact, good preventative maintenance begins crossing over into what’s known as predictive maintenance.
Predictive Maintenance for Construction Fleets
Predictive maintenance seeks to use accurate and detailed data to decide when and how to perform equipment maintenance. Predictive maintenance differs from preventative maintenance in that it seeks to use all resources to formulate a holistic prediction of how long an individual piece of equipment or part will last. This is especially important for heavy equipment maintenance when you’re dealing with high-dollar repairs.
With modern sensors and tracking systems, construction managers can evaluate the individual components of the vehicle and its routine (or irregular) utilization, getting a much better read on whether the vehicle needs to be pulled in for maintenance. With predictive equipment maintenance, instead of using generally accepted guidelines, construction companies can receive real-time hours or miles data.
How does a construction company achieve this level of maintenance efficiency? It requires forward-thinking and the adoption of modern tools that allows them to keep a detailed equipment maintenance log based on real and reliable asset data.
For predictive maintenance to function as it should, it requires a high degree of visibility and governance over the fleet. This is typically achieved using strong equipment asset tracking programs, onboard vehicle telematics, and scheduled testing of the equipment and its parts.
Now, let’s talk about the practical steps to implementing a strong construction equipment maintenance program.
Reduce Equipment Cost: Building a Construction Equipment Maintenance Program
This section will discuss several components of good equipment maintenance software. A total equipment maintenance solution can help contractors manage their preventative maintenance and work towards predictive maintenance.
Here Are the Components of a Good Equipment Maintenance Program:
- Software. The brain of the program, it collects and analyzes information about equipment fleet assets, synthesizing it into meaningful data in a single place.
- Equipment monitoring tools. These are the nerves of a good maintenance program. Equipment monitoring sensors communicate information back to the brain, ensuring managers have a clear picture of their fleet.
- Integrated platform. The platform is the body, it holds everything together, allowing each corner of the company to access the equipment data in web or app form and function in step with the other team members. It can also integrate with other key software or systems to share data.
Below, we’ll look at each of these three pillars of a strong construction fleet maintenance program individually.
Construction Equipment Maintenance Software
There are several levels of equipment maintenance; how you implement these maintenance systems depends on your technology. Think about software as the central nervous system of your system – the brain and spinal cord. Your software platform will synthesize and organize all the outside information from the field – compiling reports, sending alerts, and predicting potential outcomes.
Aside from a strong management team, your software is the foundation of an equipment maintenance program.
Here Are the Marks of Good Equipment Maintenance Platforms:
- Targeted at construction. Construction teams need software solutions that are built for them, and they particularly need software built for heavy equipment maintenance. While many large-scale tech companies offer services to construction, few of them understand the nuances of the construction industry.
- Scalable and customizable. Each company has specific needs. Good software will fit the company, not forcing the company to fit the software.
- Allows for integration, harnessing the power of IoT. The Internet of Things (IoT), is the idea of a connected workforce. Just as smart-homes have become popular, a “smart” construction workforce keeps everything connected.
- Accessible. The software system should be, ideally, accessible by anyone authorized to access that information. This is extremely helpful for keeping teams connected and ensuring different positions have the information they need to get their jobs done individually and advance the team collectively.
If the software is the brain, the field tools are the peripheral nerves that deliver information. Let’s talk about how innovative field tools can keep your fleet connected, giving you an advantage when it comes to equipment maintenance.
Equipment Maintenance Tools to Provide Fleet Maintenance Solutions
This section will highlight how monitoring equipment can reduce construction maintenance costs. In the construction industry, there is a requirement for durable, simple, and connected monitoring equipment.
Here Are a Few Tools That Can Vastly Improve the Coordination of an Equipment Maintenance Program:
- Digitized inspections. When simple inspection sheets are digitized, this information can be sent directly to the managers. This allows anything flagged in the daily inspection to be immediately brought to attention and corrected, preventing a delay in corrective action and ongoing or worsening problems. Digital inspection sheets are the best way to keep your information accurate, and they allow you to customize the inspection sheet to every vehicle or machine’s needs. Finally, you can ensure the inspection sheets are being completed on time, not after the end of the workday.
- Telematics. On board equipment and vehicle telematics enables real-time remote heavy equipment and fleet monitoring. These modern tools can plug into the asset’s computer system, transmitting a host of data about its internal health and status, including hours/miles, fault codes or other warnings, and more about the asset’s current status and condition. Leveraging telematics via GPS and other equipment trackers also enables businesses to track equipment in real time. This allows managers to play the most coordinated game of musical chairs when they need to rotate a piece of equipment out for maintenance. The use of trackers can increase uptimes by allowing the managers to carefully monitor utilization on their jobsites.
- Driver scorecards. Driver scorecards can be put in place to coach drivers to drive more safely. Eliminating behaviors like hard braking and idling can eliminate excessive wear and tear on vehicle assets and provide more time between needed maintenance with better operation and handling. These tools can further improve equipment maintenance monitoring and reduce equipment costs and liability.
Modern tools like worksite Bluetooth trackers, QR readers, and mini-trackers allow for much more detailed control of a fleet.
Integrated Platform: Paramount for Heavy Equipment Maintenance Management
We’ve talked about the equipment tracking devices as the nerves and equipment maintenance software as the brain. But now we need to talk about the body that ties everything together: integrated software platforms and systems.
Integration is both a connected software system and the concept of a unified team. While a single platform will allow integration of multiple components, such as all a contractor’s asset types, modern integration is pushing the boundaries, allowing separate platforms, such as your equipment management system and your ERP or project management system, to form a strong connection by communicating key information.
Keeping all your equipment on an integrated maintenance system that supports use cases for all the relevant roles in your business allows your team in the field to seamlessly communicate with the maintenance department, your team in the office to easily correspond with the team in the field – and that they all stay connected.
Integration is often the key to enabling this connectivity between other systems. Just as Google products seamlessly integrate services like email, docs, and video, construction companies must enhance connectivity to obtain the most out of their heavy equipment maintenance solutions. Heavy equipment maintenance integrations connect a single platform with other systems, allowing the transfer of data between each.
Why Equipment Fleet Maintenance Matters for Construction Teams
When thinking about maintenance, it can be easy to fall for an illusion. This illusion believes that wasting time on a bunch of repairs and maintenance will only disrupt workflow and cost money; however, as the saying goes "It costs just as much to keep your gas tank full." Those who keep their gas tank full are never in danger of stalling on the side of the highway.
Likewise, the construction company that chooses to stay ahead of its maintenance needs will be able to stay on task. Aside from the obvious inconvenience and cost of repairs, there are more subtle dangers and costs to subpar maintenance. If a smaller asset like a walk behind compactor goes down, it's a smaller loss, but when a paver or bulldozer fails, this can cause hazards on an active jobsite and there is a significant cost of downtime.
Downsides of a Poor Construction Maintenance Program:
- Repairs cost more. The cost of repairs tends to be more than preventative maintenance. Buying new is sometimes effective, but if you’re losing years and years from a piece of equipment you would have saved money maintaining it. Maintenance is all about the long game.
- Cost of Downtime. As stated, downtime costs more than just the repair. Downtime means productivity stops, replacements need to be secured, workers are idle, and all this results in cost impacts. The more repair and lost productivity, the greater the overall cost of ownership.
- More safety hazards. When maintenance is sub-par, safety risks increase. Not only does this result in unfortunate worker injuries, but it can lead to expensive legal issues, OSHA safety rating, and a marred reputation. Good equipment maintenance and safety monitors can mitigate these risks.
- Decreased worker satisfaction. It's currently a tough labor market, with many construction companies scrambling to find talented, experienced people to build their jobs. Not only does healthy and well-maintained equipment make the worker's job easier and more sustainable, but it also gives workers satisfaction, knowing they are getting the job done and reducing frustrations when unusable resources hold them back.
- Overstock and overbuying. In the construction world, there are already enough variables - weather, changing laws, hidden expenses. Frequent breakdowns caused by poor maintenance may lead to the purchase of unneeded replacement parts or consumables and an eventual overstock. Consequently, these additional purchases and carrying costs add up and could be avoided with better maintenance and utilization of existing assets. Contractors need strong equipment inventory maintenance software to ensure they are placing their dollars where they are most needed.
Construction businesses rely on their equipment. Investing in proper maintenance for your heavy equipment will always pay off.
Conclusion: Equipment Maintenance Solutions for Construction Equipment and Vehicles
Construction equipment must perform within the most demanding environments and conditions and deserves high priority when it comes to maintenance and repair. In an industry known from slim margins, it’s extremely important to have a robust maintenance program.
In addition to the requirements for safety, maintenance costs can skyrocket when repairs and services are mishandled. It's important that every construction manager look at their equipment maintenance system and ask themselves what's working and what is not. Many of the construction industry’s modern maintenance troubles can be traced to a lack of adoption of digital innovations and fully integrated solutions.
Changes in the world have forced everyone everywhere to adapt, and construction is no exception. Those with a smart, efficient maintenance program will weather the storms and maintain a competitive advantage.
Contact Tenna to discover how their equipment maintenance services will help you manage your construction fleet to avoid down-time, increase productivity, and cut out all wasted repair costs.
About Kristen Olson
Kristen brings experience her diverse experience with The Conti Group to Tenna. From her involvement with essentially every facet of the organization, to start-up initiatives within Conti, with specific organizational change projects to over 17 years focused in Human Resources, she has firsthand knowledge and understanding of the industry and contractors Tenna serves. Her creative mind and non-traditional background results in innovative solutions to the programs, procedures, and standard human resource responsibilities as she works with the various departments within Tenna while always focusing on Tenna’s current and future customers.