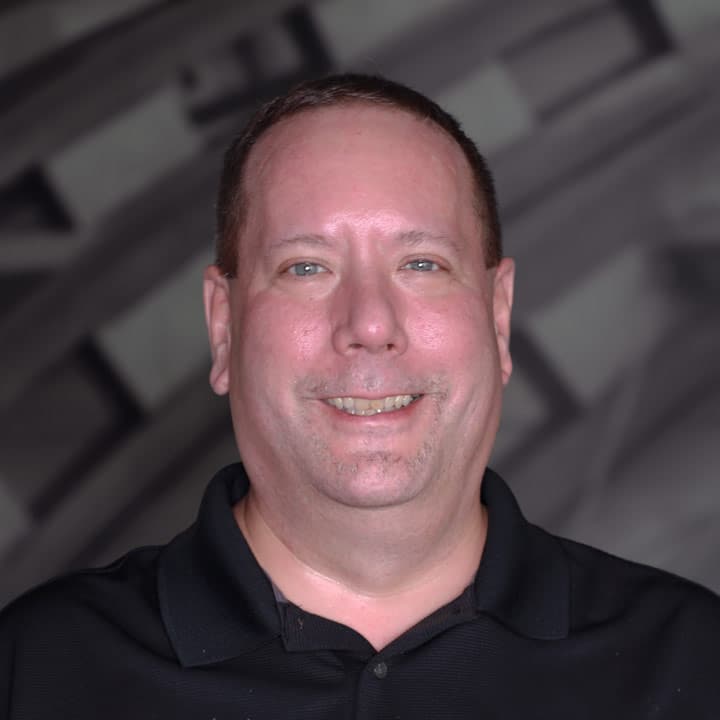
We get asked for a “rugged tracker” a lot. Understandably so, given our customers are contractors and the construction environment is rough.
While there are a lot of claims on the market regarding the ruggedness of a tracker, they may not truly be rugged enough to withstand the harsh environmental conditions these trackers are subjected to on jobsites during each season. Here are the four components that we have determined make up a rugged tracker:
1. Ingress Protection (IP) Scale
IP Scale (ratings) are defined in international standard ANSI/IEC 60529. The rating is used to define levels of sealing effectiveness of electrical enclosures against intrusion from external elements you’d find outdoors like dust, water and particulates as examples.
The numbers that follow the IP Scale each have a specific meaning.
- The first indicates the degree of protection (of people) from moving parts, as well as the protection of enclosed equipment from foreign bodies (dust and particulates).
- The second defines the protection level that the enclosure enjoys from various forms of moisture (water and submersion).
Deciphering the ratings, which range from 0-6 for intrusion protection and 0-9 for moisture protection:
First Digit is for intrusion protection
- No special protection. Not rated (or no rating supplied) for protection against ingress of this type.
- Protection from a large part of the body such as a hand (but no protection from deliberate access); from solid objects greater than 50mm in diameter.
- Protection against fingers or other object not greater than 80mm in length and 12mm in diameter (accidental finger contact).
- Protection from entry by tools, wires etc., with a diameter of 2.5 mm or more.
- Protection against solid objects larger than 1mm (wires, nails, screws, larger insects and other potentially invasive small objects).
- Partial protection against dust that may harm equipment.
- Totally dust tight. Full protection against dust and other particulates, including a vacuum seal, tested against continuous airflow.
Second digit is for moisture protection
- No protection.
- Protection against vertically falling droplets, such as condensation. ensuring that no damage or interrupted functioning of components will be incurred when an item is upright.
- Protection against water droplets deflected up to 15° from vertical
- Protected against spray up to 60° from vertical.
- Protected against water splashes from all directions. Tested for a minimum of 10 minutes with an oscillating spray (limited ingress permitted with no harmful effects).
- Protection against low-pressure jets (6.3 mm) of directed water from any angle (limited ingress permitted with no harmful effects).
- Protection against direct high-pressure jets.
- Protection against full immersion for up to 30 minutes at depths between 15 cm and 1 meter (limited ingress permitted with no harmful effects).
- Protection against extended immersion under higher pressure (i.e. greater depths). Precise parameters of this test will be set and advertised by the manufacturer and may include additional factors such as temperature fluctuations and flow rates, depending on equipment type.
- (K): Protection against high-pressure, high-temperature jet sprays, wash-downs or steam-cleaning procedures - this rating is most often seen in specific road vehicle applications (standard ISO 20653:2013 Road Vehicles - Degrees of protection).
*DSM&T provides simple and comprehensive information on IP Ratings as well as a summary chart.
Examples
Here are the minimum IP ratings we recommend for construction equipment tracking devices to be considered “ruggedized”. Based on what we just learned, the higher the rating, the more rugged.
- IP65 Enclosure - IP rated as "dust tight" and protected against water projected from a nozzle.
- IP66 Enclosure - IP rated as "dust tight" and protected against heavy seas or powerful jets of water.
- IP67 Enclosures - IP rated as "dust tight" and protected against immersion. for 30 minutes at depths 150mm - 1000mm
2. G Force Tolerance
A tracking device may be subject to jarring events on occasion caused by falling stones, equipment dropping, impacts from swinging crane elements, etc. A rugged tracker must tolerate these events and remain functional. Impacts or movements exerts a force. These are measured by acceleration detectors in the tracker that can also resolve direction of the exerted force (up/down, left/right/ and side to side). There are significant amounts of complexity behind each of these but together they can provide essential data for a business. The data can provide accident documentation as irrefutable evidence of impact or movement events, which can expose a driver’s behavior, identify the force of a collision, and/or show when there is abuse by operators. What is the recommended measurement or limit of g-force tolerance to be considered “rugged”? Generally, a tracker must be able to withstand at least 5G repetitive accelerations without damage or a malfunction.Example
A heavy load drops into a dump truck causing a sudden shudder (which must not damage or dislodge the tracker). In this example, the dump truck was subjected to a downward force from the impact of the falling load and would be recorded by the tracker.
3. Temperature or Environmental Resilience
The environmental resilience of a tracker has a lot to do with the type of battery and casing and is generally measured at -40◦F to 140◦F for those trackers that contain a rechargeable battery. A rechargeable battery, like a lithium ion battery must not be recharged in subfreezing temperatures because it will cause damage and compromise safety. For this reason, charging must be inhibited at subfreezing temperatures. At temperatures above 140◦F, lithium-ion batteries must not be charged, to avoid the possibility of thermal runaway which can destroy the battery and tracker. The battery management system provides this protection by monitoring battery temperature. Non-rechargeable batteries, such as lithium metal, can handle wider temperature extremes (-67◦F to 185◦F) and are more effective for tracking devices where an infrequent reporting schedule like once a day is suitable. Casings that are part of the tracking device can help with either end of the temperature extremes by providing a degree of isolation from the environment.The case material itself, it’s coloration and construction also are influenced by environmental extremes. The material must be able to handle high temperatures without deformation and low temperatures without cracking or shattering. How fast it heats up in the sun is influenced by its color so picking a lighter color can help reduce heating effects. The case material selected must resist ultraviolet light to avoid rapid aging in the sun which causes yellowing, cracking and case failure. Similarly, for low temperature applications, the case must not become brittle to avoid cracking under impact or large accelerations. A sufficiently rugged case can be constructed using Glass-Filled Nylon, ASA or ABS plastics.
Given the temperatures that are present in construction environments, the battery should be a non-rechargeable lithium metal one and be in a casing that can support the extremes in temperature that a piece of equipment or the environment can present.
4. Electrical Interface
For a tracker, this is the connection of a device to the vehicle or piece of equipment and the device’s ability to withstand voltage extremes that occur in the equipment’s electrical system during normal and in failure modes. The use of an OBD or JBUS connected tracker, or any tracker that accesses the vehicle electrical system like trailer trackers, must be able to withstand transient voltages present in the vehicle electrical system. Following recommendations in ISO7637 ensures best practices.
The larger the voltage spike, the more potentially dangerous to any attached equipment like trackers. Rugged trackers must be designed to tolerate these transients without suffering electrical damage.
Conclusion
While this is a very complex answer, we hope that it has provided you with the basics on understanding on what goes into determining a trackers durability. We also hope this has given you an increased awareness on the intricacies that must go into making a tracker rugged enough to withstand the rigor of construction environments. Next time you are in the market for a rugged tracker, you will know what to look for.
About Frank Rodriguez
As the Hardware Engineering Manager, Frank works tirelessly to build Tenna’s tracker ecosystem. Leveraging contacts across industry, and vast experience in the electronics industry, Frank brings new ideas, opportunities, and capabilities to Tenna’s growing list of asset trackers, and works with Tenna’s customer success personnel to bring that value to customers. Frank has worked in a variety of technical settings in his 35+ years in electronics. Frank is a published Scientist, with 5 peer reviewed publications ranging from IoT Smart City innovation to tagging & tracking individual cells using IC chips. Frank holds 10 patents spanning a range of products and technologies, most of which resulted in profitable mass market products.