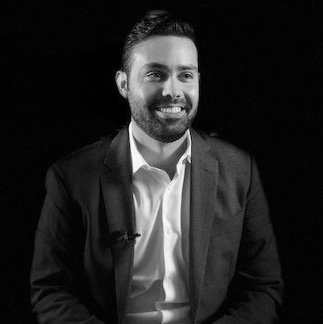
In the construction industry, managing heavy equipment and mixed fleets is complex. Delays, equipment misuse, safety incidents, and operational inefficiencies can lead to significant cost overruns and project setbacks.
That’s where a telematics system comes in—a powerful tool that combines data, technology, and automation to transform how construction businesses manage their equipment and operations.
Telematics systems are quickly becoming a mainstay in construction fleet management. They help contractors track equipment in real-time, monitor performance, improve safety, and maximize usage. Seems like a no brainer.
In this guide, we’ll explore the fundamentals of telematics, how telematics systems benefit construction operations, and why it’s essential for future success in this industry.
What is a Telematics System?
A telematics system is a technology that uses GPS, sensors, and wireless communication to collect and send real-time data from construction equipment and vehicles.
Telematics systems gather information on:
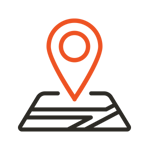

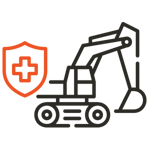
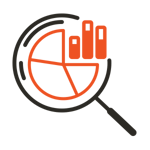
➡️ For a detailed explanation, check out our full guide: What is a Construction Telematics System.
These systems provide construction managers with a detailed view of their fleet and enable data-driven decision-making.
The Role of Telematics in Construction Equipment Management
In construction, telematics systems play a crucial role in:
- Monitoring fleet location and activity to improve equipment allocation
- Reducing downtime through proactive maintenance alerts
- Enhancing operational efficiency by analyzing equipment usage and performance
- Finding better ways to optimize owned assets and make better decisions on renting, purchasing and selling
- Identifying opportunities to unload assets from the fleet
- Ensuring compliance with safety regulations
Telematics systems give construction businesses real-time insights and control over their assets, which equals smoother operations and increased profits.
Key Features of an Effective Telematics System for Construction
A successful telematics system should provide contractors with more than just location tracking. It should offer a full suite of management and analytical tools.
Here are the key features that define an effective telematics system for construction businesses:
Real-Time GPS Tracking and Monitoring
This is foundational for a telematics system. Real-time GPS tracking for construction equipment allows contractors to monitor the location and movement of every piece of equipment in their fleet.
This helps make sure that machines are used when and where they are needed. It also reduces idle time and improves asset security.
Natively Built within Equipment Management Software
A powerful telematics system should be built seamlessly within an overarching construction equipment management platform.
Centralizing this information on single platform provides a single view of equipment location, maintenance status, job progress, and cost tracking for total visibility and ease of use.
Equipment Maintenance Alerts and Predictive Analytics
Telematics trackers can check engine health, fluid levels, and performance. They send maintenance alerts before equipment breaks down.
Predictive maintenance helps reduce repair costs and minimizes unexpected downtime.
Equipment Utilization Metrics and Performance Dashboards
Tracking how equipment is used allows you to identify underutilized assets, spot operational inefficiencies, and make data-driven decisions about fleet size and composition.
Performance dashboards provide clear, actionable insights for fleet optimization.
Construction Dispatching and Resource Sharing
Contractors can track the location of equipment and monitor its usage. This helps them share resources better.
They can move underused equipment to places where it can be used more. Machines can also be brought in for service and repairs when they are not in use. This ensures the shop is always deploying well-maintained machines into the field.
Safety and Compliance Management
Telematics systems support ELD and IFTA compliance through fleet tracker data. They also work with safety AI dash cams. These cameras monitor vehicles and equipment both on and off the road.
How Telematics Systems Benefit Construction Operations
Telematics systems are not just about tracking—they directly impact the way construction businesses operate and, ultimately, compete. Here’s how:
Streamlining Dispatch and Scheduling Processes
Knowing where your equipment is at all times is important. It helps you know if it is in use on a jobsite or down for maintenance. This information allows for quicker and more accurate dispatching and scheduling.
Equipment and logistics managers and dispatchers can quickly identify the closest available equipment, avoid conflicts, and maximize resource allocation across job sites.
Enhancing Safety and Compliance on Job Sites
Equipment trackers and cameras in telematics systems help improve safety. They monitor operator behavior and find dangerous or wasteful patterns. They also send real-time alerts for equipment misuse or unauthorized use.
This ensures compliance with safety standards and reduces accident risks. The same goes for fleet trackers and cameras for on-road vehicle operation.
Optimizing Fleet Utilization and Reducing Downtime
Telematics systems help construction companies track equipment use. They identify idle assets and fuel waste trends. This helps improve uptime and overall use of owned assets. It also reduces the need for expensive rentals or extra purchases.
Implementing a Telematics System in Your Construction Business
Adopting a telematics system into a construction business requires careful planning and execution for the best chances of adoption. Follow these high-level steps to ensure a successful rollout:
- Assess Your Needs: Identify the equipment in your mixed fleet. Determine the data points or insights you want to track. Focus on individual fleet assets and overall fleet trends over time.
- Select the Right Telematics Provider: Pick a system made for construction. It should track your mixed fleet. It must work well with your current workflows, construction management software, and ERP. Also, choose a provider you trust for customer support.
- Install Hardware and Certify your Mechanics: Use a project management approach to install tracking devices on your fleet. This will help manage all asset types at different site locations. Train your mechanics to install, verify, and troubleshoot telematics devices within your equipment fleet.
- Configure Software and Train Your Team: Make sure the telematics platform has the right permissions and access levels. Create reports and alerts for data analysis. This will help you get timely notifications for issues that need immediate attention. Provide training for operators, site managers, mechanics, accountants, and others who will use the system. This will help everyone understand how to use the system for their specific tasks.
- Monitor and Adjust: Look at performance data and improve processes for the best efficiency. Make sure you are tracking the KPIs you set when you started the project. Make sure your telematics provider meets with your team regularly. This will help ensure you get support, see results, and receive the most value from the system.
Best Practices and Common Pitfalls of Implementing a Construction Telematics System
-
- Start small and take a scaled approach to installing hardware across your mixed fleet, and training your users in segments.
- Choose a system that is flexible to grow with you as your fleet grows.
- Make sure all stakeholders agree on the goals and benefits of the system. They should also understand why the team is implementing it.
- Don’t overlook employee training—knowledge gaps and lack of transparency can reduce adoption rates.
- Avoid overcomplicating the system with too many data points. Focus on actionable insights.
Overcoming Challenges in Technology Adoption
Resistance to change is natural, especially in the construction industry where tech adoption has been historically challenging. Clear communication about the benefits of telematics is important. Offering hands-on training can help the team adjust to the change.
Work closely with your telematics provider to address technical issues quickly and keep operators engaged.
Best Telematics Providers for Construction Businesses
When choosing a telematics provider for your construction business, consider a few important factors. Look at the provider's experience in the construction industry, and check if their solutions can grow with your business.
Also, review the products and features they offer, such as equipment use, maintenance scheduling, dispatching, and safety monitoring.
Here are the best choices for construction businesses that want to use telematics or change to a better provider:
Tenna
Tenna offers a telematics solution for construction, designed to track mixed fleets and improve equipment utilization, maintenance, and job costing. Tenna’s platform integrates tracking, maintenance alerts, financial insights, and compliance tools into a single interface—tailored for construction operations.
Tenna has become a go-to solution for many construction companies because it combines the best of fleet tracking, asset management, and operational insights into one construction-specific platform. Its ability to handle mixed fleets (owned, rented, and third-party equipment) also makes it very appealing for large and complex construction projects.
Having all our telematics data filtered onto One Platform makes it such an incredible tool. I can train my team on one tool, reducing training, eliminating extra passwords, and leading to more uptime. It’s so much easier to go to one interface and have everything you need at your fingertips.” - Project Engineer, Severino Trucking
HCSS
HCSS offers equipment management and telematics solutions focused on streamlining job site operations and improving data accuracy. The brand has concentrated solely on software solutions for the construction sector since the 1980s, gaining extensive industry expertise.
Track Unit
Track Unit is a strong choice for contractors with both heavy equipment and smaller tools. It excels in predictive maintenance and equipment uses and focuses on the construction industry. With many OEM integrations, Track Unite focuses primarily in Europe but has a growing presence in North America.
In Conclusion: Telematics Systems Are a Must-Have for Construction Businesses
Telematics systems have become a must-have for modern construction businesses. From real-time GPS tracking to predictive maintenance and data-driven fleet management, a telematics system provides the tools and data contractors need to stay competitive in today’s fast-paced environment.
Tenna stands out as the leader in construction telematics offering a comprehensive platform that integrates seamlessly with operations, reducing costs and improving equipment utilization.
Ready to unlock the full potential of your fleet? Connect with Tenna today and take control of your construction operations with industry-leading telematics technology.
About Austin Conti
As CEO and Co-Founder of Tenna, Austin leverages his international experience in construction operations for civil, building, and energy projects with The Conti Group, which has built successful, reputable businesses that make a positive impact on the world in construction, engineering, renewable energy, real estate, technology, and biotech. His passion for entrepreneurship led him to create a construction technology platform built on over a century’s experience from The Conti Group.