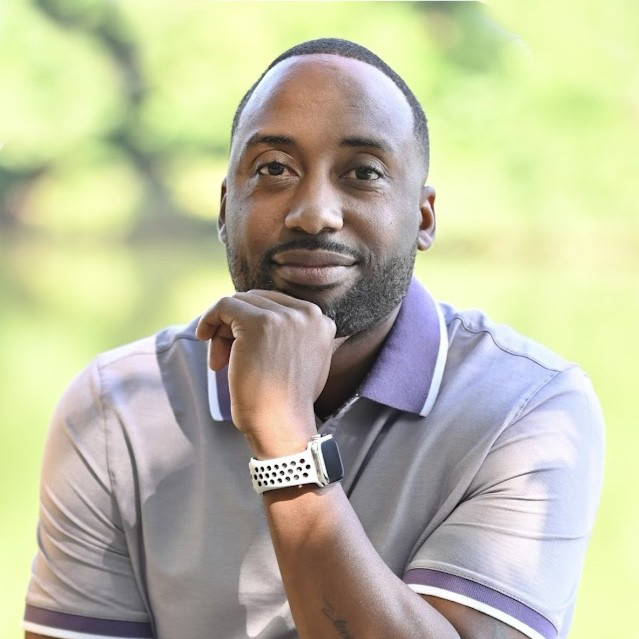
Keeping equipment running smoothly is crucial for successful construction operations. Downtime isn't just an inconvenience; it's a costly disruption that can derail projects and impact your bottom line.
That’s why forward-thinking contractors are using maintenance management systems. These systems help make maintenance easier, cut downtime, and increase equipment life.
But, with a plethora of software options available, how do you choose the right one for your construction business?
Let's dive into a comprehensive analysis of the top maintenance management systems tailored for the construction industry.
What is a Maintenance Management System?
A computerized maintenance management system, also known as a CMMS, is software that helps organizations manage their maintenance tasks. It allows them to schedule, track, and document the upkeep of assets. This includes heavy equipment and fleet vehicles used in construction.
These systems support preventative maintenance, work order management, inventory control, inspections, and more.
Why Maintenance Management Systems Are Essential for Construction
The Best Construction Equipment
Maintenance Software
Learn what important features equipment maintenance software should have and how using it can impact your construction business.
These systems keep assets running, automate service schedules, lower repair costs, and gather maintenance data. This is important for the complex and mobile nature of construction fleets.
Construction equipment faces harsh conditions, requiring meticulous upkeep. A well-implemented maintenance management system offers:
-
- Preventative Maintenance Scheduling: Reduce unexpected breakdowns through scheduled maintenance.
- Asset Tracking: Keep a close eye on equipment location, usage, and condition.
- Work Order Management: Streamline repair requests and track progress.
- Inventory Management: Manage spare parts and supplies efficiently.
- Data-Driven Insights: Gain valuable insights into equipment performance and maintenance costs.
Top 9 Maintenance Management Systems
1. Tenna
Overview: Tenna is a construction-specific equipment management platform that stands out with its deep industry expertise and integrated asset tracking, telematics, dispatching, safety and compliance, and maintenance management capabilities.
Pros:
- Built for construction teams by construction pros.
- Integrated with telematics and GPS for real-time condition monitoring.
- Maintenance records are tied directly to each asset.
-
Parts inventory management feature enables contractors to request parts, manage cost tracking for parts, and control inventory delays.
-
Time card solution for mechanics to capture time against sites, assets, work orders, and maintenance requests.
- Mobile app for field use.
- CMMS features integrated with broader equipment management tools.
- Excellent customer support.
Cons:
- Focused primarily on medium-to-enterprise contractors.
- May have a learning curve for teams new to digital systems.
Pricing: Custom pricing based on fleet size and feature needs.
Best For: Mid-to-large contractors seeking an all-in-one construction operations platform.
2. Limble CMMS
Overview: Limble is a general-purpose CMMS designed for a wide range of industries. Many users recognize it for its user-friendly interface and fast setup.
Pros:
- Intuitive dashboard and mobile app.
- Easy to create and track work orders.
- Asset hierarchy and QR code scanning are available.
Cons:
- Not construction-specific; lacks field equipment tracking or jobsite context.
- Integrations may require customization for construction workflows.
Pricing: Starts at $35/user/month.
Best For: Companies looking for an easy-to-use general CMMS with flexible customization.
3. MaintainX
Overview: MaintainX offers a modern, mobile-first CMMS with strong team communication features. Popular in manufacturing and facility management, it is gaining traction in construction.
Pros:
- Strong mobile interface.
- Real-time chat and team collaboration built in.
- Good for maintenance checklists and inspections.
Cons:
- Not tailored to construction-specific workflows or equipment types.
- Limited GPS or telematics integration.
Pricing: Free tier available; paid plans start at $16/user/month.
Best For: Teams looking for a communication-forward maintenance tool.
4. Fleetio
Overview: Fleetio focuses on fleet management and maintenance, offering digital vehicle inspections, service reminders, and fuel tracking. It’s well-suited for contractors with large vehicle fleets.
Pros:
- Strong fleet and vehicle management tools.
- Preventative maintenance scheduling.
- Fuel and cost tracking included.
Cons:
- Limited support for yellow iron and construction equipment nuances.
- Requires third-party telematics for full functionality.
Pricing: Starts at $4/vehicle/month plus optional add-ons.
Best For: Contractors with a strong emphasis on vehicles and light fleet.
5. UpKeep
Overview: UpKeep is a mobile-first CMMS designed for a wide variety of industries. Customers recognize it for its flexibility and ease of implementation.
Pros:
- Simple work order creation and tracking.
- Photo uploads and document attachments.
- Helpful reporting dashboard.
Cons:
- Not tailored to construction asset tracking.
- Limited integration with heavy equipment telematics or GPS.
Pricing: Starts at $45/user/month.
Best For: Smaller teams or companies starting with digital maintenance.
6. HCSS Equipment360
Overview: HCSS is a staple in the construction software space, and Equipment360 is their heavy equipment maintenance solution. It integrates with other HCSS products like HeavyJob.
Pros:
- Purpose-built for construction equipment.
- Seamless integration with job costing tools.
- Strong support and onboarding.
Cons:
- Complex interface and setup process.
- Requires integration with other HCSS products for full value.
Pricing: Custom pricing.
Best For: HCSS users and large contractors with dedicated equipment managers.
7. Fiix by Rockwell Automation
Overview: Fiix is a cloud-based CMMS that offers a user-friendly interface and robust features.
Pros:
- AI-powered maintenance insights.
- Solid work order, inventory, and asset management.
- Enterprise-grade capabilities.
Cons:
- Not built for construction workflows or mobile field crews.
- Expensive and complex for smaller firms.
Pricing: Starts at $45/user/month.
Best For: Enterprises and companies needing advanced analytics.
8. eMaint by Fluke
Overview: eMaint is a comprehensive CMMS that offers a wide range of features for maintenance management.
Pros:
- Custom dashboards, reports, and workflows.
- Scalable for multiple locations or divisions.
- Integrates with sensors and IoT.
Cons:
- Overkill for small to medium-sized contractors.
- Not construction specific.
Pricing: Starts at $33/user/month.
Best For: Large organizations seeking highly configurable CMMS.
9. AssetWorks Maintenance Management
Overview: AssetWorks offers a suite of asset management solutions, including maintenance management software.
Pros:
- Comprehensive asset management features.
- Good for managing large and complex asset portfolios.
- Strong for government and large companies.
Cons:
- Can be very complex.
- Can be expensive.
- May be overkill for smaller construction companies.
Pricing: Contact AssetWorks for a quote.
Best for: Public works, DOTs, and large fleet-based construction operations.
Final Thoughts: Which Maintenance Management System is Right for You?
Choosing the right maintenance management system depends on your fleet size, equipment types, team workflows, and need for real-time visibility.
When selecting a maintenance management system, consider:
- Industry-Specific Needs: Does the system cater to the unique challenges of construction?
- Scalability: Can the system grow with your business?
- Integration: Does it integrate with your existing software?
- Ease of Use: Is the system user-friendly for your team?
- Budget: Does the pricing align with your budget?
For construction companies that want to combine asset tracking, field visibility, and equipment maintenance, Tenna provides a complete solution.
Book a DemoSchedule a demo with Tenna and see how our maintenance management system can help your equipment run better, reduce costs, and streamline operations.
FAQs
What is a construction maintenance management system?
Construction maintenance management systems make construction maintenance easier. They help contractors schedule equipment maintenance, track mechanic time, find parts, and submit work orders.
What features should construction businesses look for in equipment maintenance software?
Contractors should look for key features like a user-friendly interface. They need mobile access and integration with telematics and ERP systems. Customizable maintenance schedules are also important. Real-time reporting and analytics are essential too.
How does maintenance software benefit construction companies?
Maintenance management systems can help construction companies in many ways. They can lower equipment repair costs and extend equipment lifespans. These systems also minimize downtime and improve safety compliance. Additionally, they can increase the resale value of equipment.
About Jaquan Green
Jaquan works closely with prospects and customers throughout the full sales cycle, from discovery to demos, proof of concepts, and implementation, showcasing the value of Tenna's construction equipment technology. He provides feedback for product and process improvements, collaborates with Engineering and Product teams on platform updates, and leads internal training as a Subject Matter Expert. Jaquan also partners with Executive Leadership on the product roadmap to drive innovation.