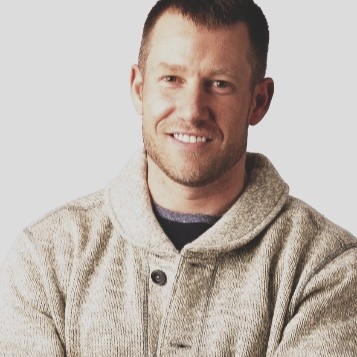
The importance of equipment management has always been critical to running a construction business. Unfortunately, business leaders are still challenged with protecting massive investments in heavy equipment, fleet vehicles, and construction materials due to inefficient and outdated processes, and not embracing innovative construction technology to make it easier.
With specialized technologies such as AI and data analytics maturing, equipment managers now have new and more effective methods to ensure they are making the most of their equipment management systems. Before understanding how equipment management has evolved and will continue to evolve in the coming years, it's important to understand the role of equipment management in construction.
What business leaders want from equipment management tools
The ability to procure equipment at a reasonable cost, and promptly
The last couple of years has brought significant challenges for equipment management teams. Between supply chain issues and rising equipment costs, equipment managers have had to find bargains through searching the used equipment market. The price of heavy duty trucks has reached its highest point in almost two decades. However, venturing into the used equipment market is not without its own challenges.
Business owners and equipment managers must understand the utility that each new asset can provide and use that information to make asset purchases that can generate a substantial return on investment. Business leaders can leverage historical data in their equipment management software to estimate the total cost of ownership of a potential purchase and justify that investment based on data about their past use of similar equipment in their fleet. In addition, when it comes time for a contractor to resell a piece of equipment in their fleet, supplying data about the maintenance of a machine from their equipment management software can help them boost their resale value.
To protect business-critical equipment from theft
Once business-critical equipment is procured, it must be protected from harm. Construction sites are often poorly secured and theft is, unfortunately, not an uncommon occurrence. Equipment theft adds costs to a project due to delays in a project’s completion date, as well as replacement costs of the stolen equipment which affects the business’ bottom line. Business leaders with the right software can leverage geofencing around sites with notifications and alerts when something is out of bounds as well as leverage GPS location information to retrieve stolen equipment.
How technology is revolutionizing construction equipment management in recent years
Modern equipment management software allows business leaders to rise above productivity challenges plaguing industry counterparts
The productivity crisis in the construction industry has been well documented over the past few decades. Equipment-intensive industries such as agriculture and manufacturing received productivity boosts from widespread digital transformation and innovations in industry-specific technology, but the construction industry has steadily declined since the 1990s. This has been the case even as construction technology grows in scope and adoption. Rapidly increasing customer demand and a shrinking workforce have added to the challenges facing the sector.
Managers are empowered to reduce costs without negatively impacting operational efficiency
The pandemic created challenges spanning from the construction supply chain to the project sites themselves. These challenges caused project costs to rise, whether from high wages for increasingly in-demand workers or rising material costs due to global material shortages. This has forced business leaders to find other areas in which to reduce expenses—often by overworking business-critical equipment to increase output or keeping large and expensive equipment for longer than recommended periods of time.
However, it is extremely important to keep the equipment’s limitations in mind. Equipment management systems can help business leaders properly define these limits and optimize spending on expensive business equipment in every area from purchase to maintenance to disposal.
And going forward…
Integration has become more important as technology stacks grow more complex
The past few years have been defined by innovation and refinement of construction technology. However, the barrage of new solutions has made the construction technology landscape more saturated than ever. As technology becomes more specialized, construction companies are likely to adopt a range of software and hardware solutions instead of a total solution.
This means that integration will play a much larger role in digital transformation projects than before. Each solution must work in conjunction with all other equipment and software that a company already owns and uses. Successful integration can also help businesses overcome information silos that have plagued the industry for years.
Business leaders must better optimize regular and predictive maintenance to ensure operations continuity
The pandemic reiterated the disruptive impact of business interruption for construction companies. Multiple lockdowns and social distancing requirements at project sites meant businesses had to be ready when they were allowed to operate again. While pandemic-induced restrictions and disruptions are difficult to predict, equipment malfunction and challenges can be easier to foresee and abate.
As equipment management systems collect more equipment data and project information, business leaders are empowered to generate detailed insight about their most important equipment. With advanced AI systems and predictive analytics, construction businesses can perform maintenance before equipment issues arise. This means they can better predict when equipment will be available for use and plan for downtime in advance.
Equipment management has grown to become an important part of running a construction business. As labor shortages and supply chain challenges continue to plague the industry, business leaders are more likely to rely on digital tools and specialized equipment to complete projects on time and under budget. Equipment that is critical to business operations must be treated with the appropriate attention and care. Equipment management software will continue to empower business leaders to do just that.
Innovative construction technology is paving the way for business leaders to protect their equipment and improve their equipment management processes. Businesses now have the availability of specialized technologies to optimize their equipment management processes; while overcoming productivity challenges, reducing costs, and ensuring operational efficiency.
Contact Tenna to learn how you can find more value within your existing fleet.
About Tom Stemm
Tom Stemm is the CEO/Founder of Ryvit, a partner of Tenna’s. He was inspired to build Ryvit when several of his clients in the construction industry had asked for some custom integration development work. At the time, Tom was part of the founding team at GadellNet (a fast-growing IT consulting firm in St. Louis, MO), and they realized that there was a significant gap in the construction tech industry – namely that, while tech purchases were high, the adoption rate of those solutions throughout all stakeholders was still lagging. After a very diligent launch process, Ryvit was born to address the rampant problem of a disintegrated tech stack in the construction technology space. Tom continues to lead a team of integration developers, application enthusiasts, customer heroes, and sales superstars on a mission to eliminate duplicate data entry and rampant data errors from the construction technology world.