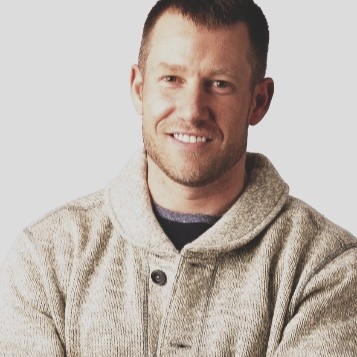
Like other technical sectors, the construction industry relies on a collection of vehicles, equipment, and specialized tools to deliver services. But, are businesses failing to treat these assets as the existential necessities they are? Equipment management systems can help business leaders get the most from the expensive equipment they invest in. For businesses to maximize the utility they receive from these systems, they must first implement an effective equipment management strategy.
How to Develop an Effective Equipment Management Strategy
Build a Business Case for an Equipment Management System
Equipment management strategies can be a tough sell to decision-makers. Many business leaders often do not have access to clear data reflecting the true costs and benefits associated with each business asset. Therefore, the areas in which an effective strategy can be useful must be understood, highlighted, and communicated.
For instance, tracking and monitoring the condition and location of each business asset from vehicles to heavy equipment can eliminate time spent searching for assets needed for critical operations, increase equipment utilization, decrease unplanned expenditures, and reduce theft. In the Pikes Peak region in Colorado alone, construction equipment theft cost businesses over $1 million in the first three quarters of 2021.
Securing your assets and knowing where they are at all times is a must for construction companies. An effective equipment management strategy has to begin with a clearly defined purpose, such as the reduction of theft, that should be communicated to business leaders to achieve full buy-in.
Understand the Unique Value and Costs Associated with Each Business Asset
Business leaders are constantly on the lookout for modern solutions that can help them cut project costs and increase profitability.
To reflect the dynamic nature of equipment value based on factors such as age and usage, an equipment’s total cost of ownership (TCO), must be taken into account. This creates a solid foundation for equipment management strategies since construction businesses are more aware of how long an asset will last and how much it will cost to use and maintain over that period.
Use Modern Equipment Management Systems and Software to Simplify Equipment Management Processes
According to a recent survey, business leaders are rapidly changing their investment strategies to accommodate the need for more technology and increasing digital transformation. Software is expected to receive as much attention and investment as hardware. Unfortunately, construction companies tend to fall behind in their adoption of digital tools; instead relying on outdated systems and poor document management. This results in inaccurate reporting, communication delays, and inefficient protocols.
Modern, cloud-based equipment management systems enable businesses to significantly streamline these processes while providing real-time access to asset data to everyone who needs it. Here’s how construction companies can make the most of their equipment management software.
How to maximize equipment utilization with an equipment management system
1. Choose Cloud-Based Solutions to Easily Access Asset Information Across Operational Silos
Construction processes are notoriously siloed. Even if you could ignore the divide between office and on-site workers, significant collaboration is still required between contractors, subcontractors, site managers, and on-site workers. Each of these stakeholders can use project resources but are often not privy to asset data that could change the way they use certain assets.
A new piece of equipment, for example, would likely be able to handle a larger workload compared to another that’s a decade old. Using a cloud-based equipment management system means every stakeholder can access important asset information and usage recommendations as relevant to their position and use cases, thereby extending the life of heavily used assets by acting from a knowledgeable and informed position.
2. Use Asset Data to Ensure Operational Assets are Yielding their Forecasted ROI
The utility of equipment management systems is more than tracking and monitoring. It also helps consolidate and analyze key performance data from a wide variety of assets. Once all equipment has been integrated into equipment management systems, business leaders can achieve full visibility of an asset’s TCO, usage statistics, location, performance, and more.
This enables leaders to analyze whether past asset purchases have delivered on the return that was forecast for them and more proactively utilize owned assets throughout their useful life. This information can be assessed by project, asset class, asset type, and even individually.
3. Adopt a Data-Centric Approach when Forecasting Business Expenditures and Planning Future Purchases
Construction businesses can expand the benefits of equipment management beyond simply making the most of and evaluating current assets. Ultimately, equipment management software is capable of delivering a wealth of actionable information to business leaders. The data that is collected, processed, and exposed via modern equipment management systems can lay the foundation to adopt a data-first approach to decision-making.
Businesses can predict the costs that will be incurred over a piece of equipment’s lifetime and weigh that against the productivity benefits that investment can bring. Knowing how much you can leverage your equipment without sacrificing quality or efficiency can also lead to more effective use of existing resources while simultaneously reducing maintenance costs.
Fully integrated and feature-rich equipment management software helps construction businesses protect their most valuable assets while extracting the maximum value that each of these assets can provide. When combined with a fully integrated technology stack, the operational data generated and shared through these systems delivers value far beyond simple maintenance and equipment protection.
Learn More About How to Maximize Equipment Utilization
If you found this information useful, please contact us to learn more about how an integrated equipment management system fits into your construction business.
About Tom Stemm
Tom Stemm is the CEO/Founder of Ryvit, a partner of Tenna’s. He was inspired to build Ryvit when several of his clients in the construction industry had asked for some custom integration development work. At the time, Tom was part of the founding team at GadellNet (a fast-growing IT consulting firm in St. Louis, MO), and they realized that there was a significant gap in the construction tech industry – namely that, while tech purchases were high, the adoption rate of those solutions throughout all stakeholders was still lagging. After a very diligent launch process, Ryvit was born to address the rampant problem of a disintegrated tech stack in the construction technology space. Tom continues to lead a team of integration developers, application enthusiasts, customer heroes, and sales superstars on a mission to eliminate duplicate data entry and rampant data errors from the construction technology world.