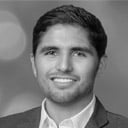
2021 was a challenging year for many businesses, but some have thrived in this daunting environment. The equipment management industry has been one such benefactor of the pandemic. Continuous business disruptions and inconsistent recoveries have highlighted the importance of managing assets deliberately and carefully.
Regardless of whether key assets are owned or rented, business leaders have learned that it is critical to business continuity that these assets are managed efficiently and properly. Here are three things that 2021 highlighted to construction business leaders about the importance of equipment management.
3 things we learned in 2021 about equipment management in construction
Productivity must continue to be top-of-mind for construction companies
The productivity issues in construction have been heavily publicized and it continues to be a major issue for business leaders worldwide. The business disruptions that construction companies faced in 2021 only exacerbated the existing problems. With widespread labor shortages and rising material costs creating havoc in project planning, it has become even more important for construction companies to extract the maximum value from the assets they own.
Business leaders must embrace digital solutions to protect key business assets
Construction demand will continue to increase in the coming years and many companies are already embracing digital solutions on and off project sites to meet this demand. With the introduction of the Infrastructure Investment and Jobs Act (IIJA) promising new project opportunities, contractors that continue to win more work will benefit from digital construction technologies that aid them in jobsite performance and balancing resources across projects more efficiently. . Modern solutions have been developed for problems that have plagued the industry for years, with technology designed to handle projects more efficiently and help compensate for labor shortages. Digital solutions have also been developed to help business leaders extract maximum value from expensive construction equipment.
Asset management solutions empower business leaders to truly know the exact cost, value, and output that businesses can expect from each piece of equipment. Construction companies rely on such equipment to keep operations running smoothly even during times of disruption. It only makes sense that business leaders invest in the protection of their most important and valuable assets.
Construction equipment theft is still a common occurrence at many project sites
One of the many challenges faced by construction businesses is the prevalence of theft at project sites. Construction project sites are often left relatively open to facilitate easy access for thieves. As a result, construction sites lose valuable items ranging from building materials to expensive equipment parts and accessories.
While the theft of common items such as simple tools is unlikely to have a significant impact on a project’s bottom line (although these costs can add up dramatically), the theft of heavy construction equipment, which accounts for over a tenth of all on-site thefts, is much more difficult to absorb. In a year that made business disruptions the norm, the loss of business-critical equipment made it even more difficult for construction companies to keep projects on time and under budget.
Why effective equipment management is key for aiding in the construction sector’s recovery
Business leaders need to make sure that key equipment is available when needed
Any business downtime, whether planned or unplanned, can cause project delays and run over budget. Therefore, construction project managers must reduce the likelihood of unplanned interruptions. While labor and supply chain issues are outside the control of business leaders, equipment malfunction and asset inefficiencies are not.
Modern equipment management software has made it easy for businesses to identify pieces of equipment that are underperforming or due for repair even before they go out of commission. This empowers project managers to plan for equipment downtime and to spread out maintenance for all key pieces of equipment.
Construction businesses can offset increased labor and material costs with cost-effective equipment management
Labor shortages and supply chain disruptions will continue to make running a construction business extremely challenging. Material costs, for example, rose sharply in 2021 and are expected to continue doing so in 2022. Labor shortages can be resolved with long-term solutions but are still expected to create issues for construction companies in the interim. This means that business leaders must find areas where costs can be reduced without negatively impacting productivity or operational efficiency.
Effective equipment management allows companies to better estimate the exact cost they can expect for a piece of equipment throughout its lifecycle based on their historical utilization data measured for other assets in their equipment management system and find areas where that cost can be reduced. Asset management software paired with a fully integrated technology stack can help businesses find avenues for cost-cutting while maintaining high levels of productivity and efficiency during a project.
Digital solutions can help protect critical business assets against theft, damage, and loss
The benefit of asset management is not limited to extracting value from important pieces of equipment. Total-solution asset management software can also empower businesses to protect assets against theft and loss. Modern technology allows each piece of equipment to be tracked at all times, giving site supervisors and project managers the location data and usage history for that asset. Even if theft or equipment damage occurs, this data allows project managers to respond to such situations quickly and effectively. This information can also be useful from a compliance perspective, giving construction companies the data they need to quickly make a detailed insurance claim should assets be stolen even after all these precautions.
Late in 2021, construction companies were able to regain some semblance of normalcy following widespread operations and supply chain disruption. However, challenges such as labor shortages, rising material costs, and inconsistent recovery have encouraged construction companies to better control the resources they have and extract the most value from assets and processes already in place.
Asset management software allows companies to do exactly that by tracking, maintaining, optimizing, and protecting their most important equipment. The digital transformation that defined 2021 will continue to disrupt the industry and as more construction companies embrace digital solutions, more will see the benefits of this innovation.
If you found this article helpful, please share it on social media. Ready to take your equipment management to the next level? Contact us to learn more.
About Jose Cueva
As Chief Product Officer and Co-Founder, Jose applies his first-hand construction experience and knowledge to deliver innovative platform solutions to a growing number of companies. His involvement in both architecting construction-specific solutions and delivering them enables him to cross over functional roles.