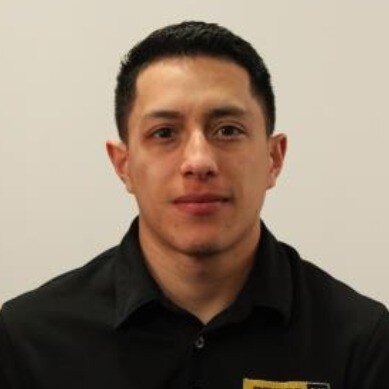
In the fast-paced world of construction, the reliability of your heavy machinery can make or break a project. Imagine this scenario: a bustling worksite where a key bulldozer is tasked with clearing debris for a critical phase of a multi-million-dollar project. One routine shift, a minor yet overlooked defect during a heavy equipment inspection spirals into a catastrophic failure.
The machine breaks down unexpectedly, halting work across the site, causing serious safety hazards, and forcing an emergency repair that costs tens of thousands of dollars. Not only does this disrupt your project schedule, but it also puts your team’s safety at risk and jeopardizes client trust.
Unfortunately, this is an all-too-real possibility for contractors. In this post, we explore a comprehensive heavy equipment inspection checklist that can help prevent such costly incidents and ensure your equipment is always ready to perform.
The Importance of Regular Heavy Equipment Inspections
For safety managers, ensuring that every piece of equipment is properly inspected is non-negotiable. A well-structured heavy equipment inspection checklist not only safeguards your workforce but also protects your bottom line from costly downtime, OSHA penalties and possible liability claims.
It is important to be proactive with your inspections so you can reduce accidents and reduce equipment downtime. Some of the most common hazards on jobsites are linked to poorly maintained heavy equipment, such as:
- Hydraulic failures leading to uncontrolled movements of equipment
- Brake and steering malfunctions resulting in collisions
- Engines overheating and causing structural failures
By implementing a rigorous equipment inspection routine, safety managers and project managers can mitigate these risks and enhance operational efficiency. They can also avoid project downtime from unplanned repairs. You often don't know about these issues until the equipment stops working.
Now, what should be included in those heavy equipment inspections? Read on to learn the requirements of your heavy equipment inspection checklist.
Creating a Heavy Equipment Inspection Checklist
Operators should start with general walk-around inspections every morning before their equipment is used.
- Look for loose or missing bolts, nuts or fasteners.
- Check tires, tracks and wheels for any wear, damage or low pressure.
- Ensure undercarriages are free of debris and obstructions.
- Check the counterweights on some of the equipment and any structural components for cracks or damage.
- Look for leaks, and check the level of fluids for engines, including coolant, hydraulic fluid, brake fluid and more.
- Finally, make sure equipment is all fueled up.
A standard equipment checklist at the start of every shift should catch all the above. This cuts problems off from becoming catastrophic failures.
For example, if operators see low fluids during a walk-around inspection, they can tell the shop. This allows them to stop work so they do not use the equipment when it is unsafe and expedites a resolution before a problem occurs.
Ensuring Operational Safety of Heavy Equipment
During these heavy equipment inspections, it is also important to start going over the safety features of heavy equipment to ensure safety and compliance. Here’s your heavy equipment inspection checklist for safety features.
First and foremost, it’s imperative to ensure emergency stop buttons and/or kill switches are functional, in case of emergencies.
Horns, warning lights and back-up alarms are probably second most important in terms of safety on jobsites and therefore must be checked regularly. If you’re out in the field, you’re actually required to honk your horn before moving the piece of equipment forward or backwards, so it’s imperative that it is working.
For warning lights, operators must examine all the fluids, checking to make sure the equipment does not have any leaks. It's important to make sure that those warning lights work in case there is an issue with the equipment, so there is a visible alert for surrounding workers.
One safety precaution that not a lot of people know about is the expiration date on seatbelts. (Yes, they have them!) So, while checking the functionality of seatbelts and harnesses, operators must also check the installation dates. Manufacturers typically recommend swapping out seatbelts every two years.
If you have fire extinguishers on your equipment, this is another check point. Operators should check the expiration date and ensure that they fill up the extinguishers. This equipment is out in the elements, and fire extinguishers need to be checked routinely more than fire extinguishers in office buildings.
Operators need to check that equipment mirrors and heavy equipment cameras work properly and that mirrors remain uncracked. Both cameras and mirrors need to be double checked for placement to ensure visibility in and around heavy equipment.
More obvious safety checks include testing brake steering and transmission. These functions must be checked before taking off at a higher speed, and parking brakes need to be checked to ensure equipment can come to a safe stop.
Transmission should be checked for smooth gear shifts. Since fluid for transmission was already checked during your walk-around, that should allow for smooth gear shifts. If not, something is wrong.
Additionally, the steering system must be responsive, so operators should ensure there isn't any lag in the system.
Lastly, operators must check lifting and hydraulic systems. They should inspect hoses and fittings, lifting mechanisms, and boom and lift arms. They need to ensure there are no cracks and verify that there is good hydraulic pressure.
Best Practices for Heavy Equipment Inspections
Now that you have your heavy equipment inspection checklist, let’s examine best practices for completing those checks. We’ve already covered standardizing heavy equipment inspection protocols with checklists, but here's what else contractors should consider:
- Using digital inspection forms and mobile apps helps with record keeping. They make it easier to use in the field and improve communication with the shop.
- Ensuring every operator follows the same checklist and inspection frequency to maintain consistency.
- Holding operators and teams accountable for ensuring safe usage of equipment.
Digitizing Equipment Inspection Forms
Many times, inspections are done on paper. If you are doing heavy equipment checks this way, you are not alone. However, as I’m sure you know, there’s a much more efficient and streamlined way to do heavy equipment inspections.
Contractors who are leveraging technology are digitizing the process with equipment management solutions like Tenna. With a digital process, safety and equipment managers can create custom inspections to ensure each machine is inspected in specific ways unique to that asset class. Operators can complete inspections directly from their phone with the Tenna app, including notes. Should an inspection criteria fail, a maintenance request is automatically created to quickly communicate with the shop about the issue for a quick resolution.
Once mechanics resolve a failed item, they can easily close the loop and alert operators. All of this can be completed without a single phone call or communication outside of an equipment management system.
Creating an equipment maintenance response plan for reporting, diagnosing, and addressing issues immediately is important for maintaining safety, jobsite productivity, and optimizing equipment uptime.
With a digital system, all team members can access the same information about heavy equipment. This includes photos and comments that document failed inspections.
By eliminating manual and paper methods, the entire inspection process becomes easier and more efficient for teams. It also eliminates the chances of losing records. With digital inspections, users log and save completed inspections. You can easily access and download them during audits or if a safety incident occurs.
Setting Equipment Inspection Checklists and Check Frequencies
With a digital heavy equipment inspection process, contractors ensure that everyone is following the same guidelines. This helps with your internal safety checks and balances. It also lets construction businesses submit compliance requirements online, often automatically.
Daily, weekly, and monthly checkups are required—each with different requirements. Be sure to set those schedules in place. If you use a digital system like Tenna, alerts will notify you when inspections are due and who is in charge.
I recommend conducting an inspection each day you use a machine. Before operating the equipment, it’s important to have a process. This process should outline what the operator needs to check.
Weekly inspections can be done by the superintendent or manager. These inspections may take more time to check all areas of heavy equipment. Monthly inspections can involve technicians to check equipment more closely.
Accidents due to equipment failure are avoidable with the proper inspection frequencies put in place.
How to Avoid Equipment Operator Negligence
Digitizing equipment inspections also helps with keeping operators accountable and uphold safety protocols. A digital system makes it easy to identify if assets have missed their required daily inspection report. With Tenna, designated safety or equipment managers are automatically notified if a scheduled or daily inspection is missed so that patterns can be detected and negligence addressed.
Tenna also provides QR codes for contractors to place on equipment to facilitate easy inspection initiation. When an operator uses a machine, they can scan the code to start the inspection before using it without having to navigate manually into the app.
Conducting random audits and holding teams accountable also represents good practice. It's critical that everyone involved understands what they must do and submit in a timely manner.
What's Most Important for Heavy Equipment Inspection Checklists?
At the end of each day, for operators, it’s about getting home safely after a day on site. For businesses, it is important to stay compliant, keep equipment running well and finish projects on time.
Having a heavy equipment checklist is crucial. However, the key part of these inspections is making them digital, connecting all teams to the inspection results through your equipment management system.
⬅️ Ready to digitize your equipment inspection process this year? Reach out to Tenna to see how our Custom Inspection functionality works.
About Miguel Aguilar
Miguel has a strong foundation in equipment software and a deep understanding of OEM capabilities. As Sales Engineer at Tenna, Miguel leverages his experience in logistics, tech support, and sales, which aligns seamlessly with his work and supports customer and company initiatives. For Miguel, life is about continual growth, as his best piece of advice reflects: “There’s always something new to learn.”