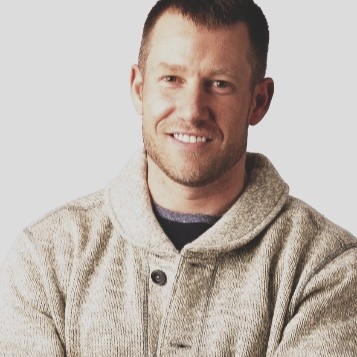
Productivity has always been a major challenge for the construction industry, as shown by the fact that annual labor productivity growth has not exceeded 1% in the last decade. A variety of factors have led to this, from a widespread labor shortage to increasing demand for construction services, to a decrease in people choosing a career in construction. However, less attention is paid to the role of equipment utilization and its impact on productivity. With more companies relying on heavy construction equipment to offset the limitations of a shrinking workforce, it has become even more important that construction equipment is well taken care of.
Unfortunately, unplanned equipment downtime and poor asset performance are common in most construction companies. Here are four reasons your key assets are not performing at optimal capacity and how technology can help you change that.
4 Common Reasons for Poor Asset Performance
1. Heavy Equipment Is Often Overutilized to Extract the Maximum Value It Can Provide
Heavy construction equipment can deliver a significant amount of value and businesses are always looking at ways to ensure that each piece of equipment delivers the maximum possible output. However, this can lead to construction teams pushing a piece of equipment to its limits. Each asset has a recommended load that it can be put under and failing to work within those constraints can expose equipment to excessive wear and tear and cause it to underperform. If leaders are not aware they are pushing their equipment too hard, they can also be caught off guard when key project assets fail and require maintenance at critical points during the project.
2. Failure to Regularly Monitor the Health and Performance of Key Assets
During construction projects, it can be difficult to keep track of all the moving parts involved. Between managing internal and external stakeholders, managing the inherent complexity of multiple, simultaneous operations and crews, dealing with equipment failure, and keeping a project on time and within budget, the operations teams are stretched thin. This results in a failure to monitor the health and performance of key assets used during the project. Without eyes on excessive use and without a set preventative maintenance schedule in place, there is a lack of visibility that can lead to breakdowns, repair needs, and related project disruptions caused by equipment failure.
3. Outdated Methods of Reporting Asset Performance Are Still Being Used in the Construction Sector
Despite the rise of integrated project management systems, construction businesses have generally been slow in adopting new technologies. As a result, communication between various departments has been dependent on outdated methods such as manual spreadsheets. Consequently, even when companies wish to collect and report asset performance data, that data that is stored and shared is incomplete or outdated.
Information silos between team members make it even more difficult for this information to be shared in a timely manner. This is further compounded when asset data is collected manually, with human error and inconsistent data collection adding to already inaccurate asset information.
4. Construction Businesses Have Been Taking a Reactive Approach to Equipment Maintenance
Construction business leaders are always looking for ways to reduce the lead time between projects. This can cause them to overlook important asset maintenance schedules as 70% of companies have done. Any downtime, even if it is planned, can cause project delays or even worse, cause the project to be put on hold and that is costly.
Failing to understand the maintenance needs of each piece of equipment can lead to further losses down the road, with unplanned downtime often costing more than predictive maintenance. Business leaders are also unable to plan around unexpected downtime, making its impact on the bottom line even more severe.
How You Can Use Modern Technology to Improve Equipment Utilization
Use a Variety of Metrics to Schedule Equipment Maintenance
It can be tempting to design a fixed schedule to conduct equipment maintenance. However, each piece of equipment has unique maintenance requirements depending on a variety of factors such as age and usage. This is even more important as construction companies purchase used equipment in response to global supply chain challenges.
Predictive maintenance software allows business leaders to monitor important performance and usage indicators to determine the best possible maintenance schedule to minimize disruption and maximize asset output. With such software, construction businesses can anticipate and solve problems before they have a chance to disrupt business operations.
Share Real-Time Insight Into the Performance of Business-Critical Assets With All Stakeholders
Business leaders often keep an eye out for a series of performance indicators that confirm if a project is on the right track. However, traditional methods of information gathering and sharing have lengthy lead times and this delay can give business and project leaders an inaccurate view of what is happening on the job site. Fully integrated equipment management systems give employees in different roles across a construction business the ability to receive and act upon real-time asset data. With modern software, they can consolidate, process, and share all asset information from a single, unified platform.
Discover and Promptly Respond to Equipment Inefficiencies
Construction teams use a range of specialized equipment on and off the project site. Each equipment has unique needs and requirements. However, project managers and business leaders are not always aware of how each piece of equipment should be maintained and cared for.
Integrated asset management systems allow all this information to be distilled into actionable and easy-to-understand recommendations, allowing business leaders to know when and how each asset should be replaced, repaired, or maintained. Advanced systems are also able to inform them of equipment inefficiencies caused by overutilization as they happen. This means project teams remain nimble and can quickly respond to inefficiencies.
Ultimately, construction businesses will have to continue to rely on a variety of specialized equipment to perform their project operations. Heavy equipment and mixed fleet assets will always be crucial for overall business continuity. With fully integrated modern asset management software, business leaders are empowered to take control of the output and health of their most important business assets—from specialized tools to heavy equipment—from a single place.
Contact Tenna to Learn More About How to Optimize Your Equipment Utilization
About Tom Stemm
Tom Stemm is the CEO/Founder of Ryvit, a partner of Tenna’s. He was inspired to build Ryvit when several of his clients in the construction industry had asked for some custom integration development work. At the time, Tom was part of the founding team at GadellNet (a fast-growing IT consulting firm in St. Louis, MO), and they realized that there was a significant gap in the construction tech industry – namely that, while tech purchases were high, the adoption rate of those solutions throughout all stakeholders was still lagging. After a very diligent launch process, Ryvit was born to address the rampant problem of a disintegrated tech stack in the construction technology space. Tom continues to lead a team of integration developers, application enthusiasts, customer heroes, and sales superstars on a mission to eliminate duplicate data entry and rampant data errors from the construction technology world.